Hygiene ist das A und O in einem Schlachthof. Deshalb achtet das dänische Unternehmen Danish Crown in seinen Schlachthöfen peinlich genau darauf, dass diese nach jeder Schicht gründlich gereinigt und getrocknet werden, ehe die Arbeit weitergeht. Der Haken: Das Trocknen der Halle verschlingt eine Menge Energie, da dafür ein starker Luftstrom und viel Wärme benötigt werden. Für den größten Schweine-Schlachthof Europas in Horsens wünschte sich Danish Crown deshalb eine effizientere Lösung, die sich einfach an den tatsächlichen Bedarf anpassen und leicht steuern lassen sollte.
Sensoren überwachen Feuchtigkeit
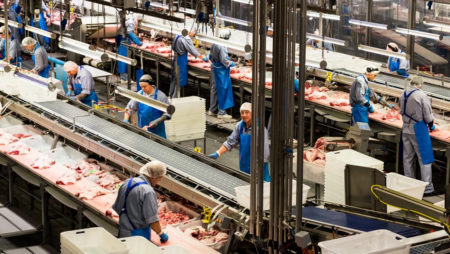
Nach jeder Schicht werden die Schlachhöfe von Danish Crown gründlich gereinigt und getrocknet, ehe die Arbeit weitergeht. (Foto | Danish Crown)
Der Energiedienstleister EnergiMidt entwickelte einen Vorschlag, wie sich die Lüftung effizienter gestalten lässt. Kern des Konzepts waren effiziente EC-Ventilatoren von ebm-papst und Sensoren, die kontinuierlich die Feuchtigkeit messen.
Ein Vorschlag, der bei Torben Andersen, Energiemanager bei Danish Crown, gut ankam: „Dieses Setting ermöglicht es uns, den Luftstrom kontinuierlich an unsere Anforderungen anzupassen. Bis dato lief unsere Anlage immer auf voller Kraft, selbst wenn am Schluss des Trockenvorgangs nur noch ein paar kleine Pfützen in der Halle übrig waren.“
In einem Pilotprojekt in einem kleineren Schlachthof in Sæby setzte Danish Crown die Kombination aus Ventilatoren und Sensoren erstmals ein.
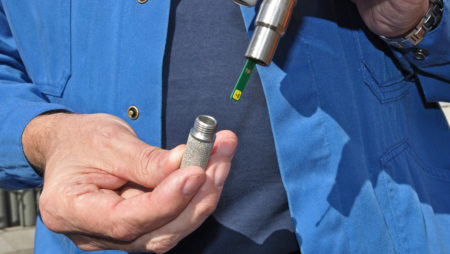
Sensoren messen die relative Luftfeuchtigkeit. Dies ist wichtig, um die Lüftung korrekt zu steuern. (Foto | ebm-papst)
Da dort kontinuierlich die relative Luftfeuchtigkeit gemessen wurde, wusste der Betreiber jeweils genau, wie viel Wärme und welcher Luftstrom nötig war, um die Nässe optimal abzutransportieren. Als Andersen danach den Energieverbrauch prüfte, traute er seinen Augen kaum. „Als wir sahen, wie viel Energie wir mit dem Pilotprojekt sparen, dachten wir zuerst wir hätten uns verrechnet. Statt der erwarteten Einsparungen von 30 bis 40 Prozent, erreichten wir fast 90 Prozent. Also erhoben wir die Daten noch einmal für eine andere Einheit und kamen zum gleichen Ergebnis.“
Bis zu 108.000 Kubikmeter pro Stunde
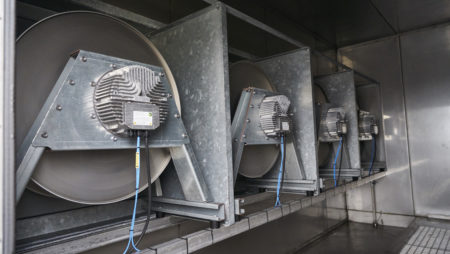
Das FanGrid mit EC-Ventilatoren von ebm-papst bewegt pro Stunde 108.000 Kubikmeter Luft. (Foto | ebm-papst)
Die Entscheidung, auch den Schlachthof in Horsens umzurüsten, fiel Andersen folglich leicht. Ein Installateur ersetze die alten durch EC-Ventilatoren von ebm-papst, die als FanGrid installiert wurden. Insgesamt 96 Ventilatoren baute das Unternehmen ein und vernetzte sie mit den Feuchtigkeitssensoren. Das gesamte System kann nun pro Stunde bis zu 108.000 Kubikmeter Luft fördern und so auch die riesige Halle trocknen. Das geschieht nun schneller und deutlich effizienter als zuvor. Andersen berichtet: „Auch an unserem Standort in Horsens konnten wir Einsparungen von knapp 90 Prozent in der Zeit realisieren, in der das Schlachthaus geputzt und getrocknet wird.“
Schreiben Sie einen Kommentar