Hygiene is everything in a slaughterhouse, so Danish Crown takes particular care to ensure that its slaughterhouses are thoroughly cleaned and dried after every shift before work is allowed to continue. What’s the catch, you ask? Drying the work areas consumes a great deal of energy as a powerful air flow and lots of heat are required for the process. Danish Crown wanted a more efficient solution for Europe’s largest pig slaughterhouse in Horsens ─ a solution that could be adapted to actual requirements and would be easy to operate.
Sensors monitor humidity levels
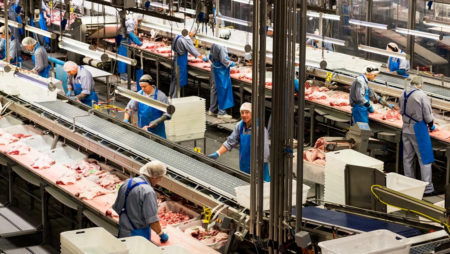
After each shift, the slaughterhouses of Danish Crown are thoroughly cleaned and dried before work is allowed to continue. (Photo | Danish Crown)
Energy service provider EnergiMidt came up with a proposal for making the ventilation system more efficient. At the heart of the concept are efficient EC fans from ebm-papst and sensors that continually monitor humidity levels.
The idea was well received by Torben Andersen, Energy Manager at Danish Crown. “This setting allows us to continually adjust the air flow to meet our needs. Before the new system was installed, the previous one always operated at full power, even if only a couple of puddles were left on the floor after drying,” says Andersen.
Danish Crown conducted a pilot test of the combination of fans and sensors at a smaller slaughterhouse in Sæby.
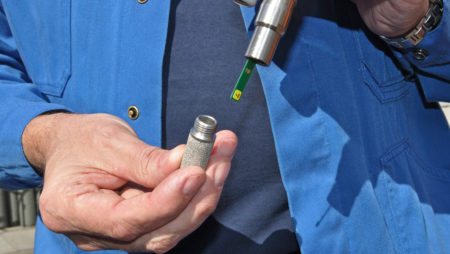
Sensors measure the relative humidity to ensure that the ventilation system is working well. (Photo | ebm-papst)
Since the humidity was continually measured there, the operator always knew how much heat and air flow were required for optimal drying. When Andersen checked the energy consumption afterward, he could hardly believe his eyes. “When we saw how much energy we were saving in the pilot, we first thought that we had miscalculated. Instead of saving the expected 30 to 40 percent, we reached almost 90 percent! So we checked the data for another unit and got the same result.”
Up to 108,000 cubic meters per hour
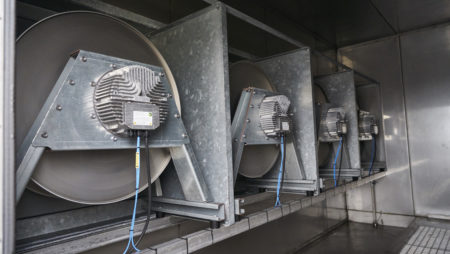
The FanGrid with EC fans by ebm-papst moves 108,000 cubic meters air per hour. (Photo | ebm-papst)
That made the decision to also retrofit the slaughterhouse in Horsens easy for Andersen. A technician replaced the old fans with EC fans from ebm-papst, which were installed in a FanGrid configuration. In total, the company fitted 96 fans and connected them with the humidity sensors. The new system can pump up to 108,000 cubic meters of air per hour ─ enough to dry even the enormous slaughterhouse. The drying process is now faster and much more efficient than before. “We were also able to reduce the energy consumed cleaning and drying our slaughterhouse in Horsens by almost 90 percent.”, reports Anderson.
Leave a comment