ebm-papst has always put its fans through their paces – but this has been taken to a whole new level since spring 2023. They are purposefully taken to and beyond their limits using real environmental influences in the testing center built in Hollenbach in just one year. New products, sizes or components pass through the test stations in a total of 6 test fields over an area of approximately 2,500 square meters. In this series, we’ll give you insights into each of these testing areas.
Erich Kemmer, who has worked at ebm-papst for more than 30 years, heads the testing center: “Our aim is to identify the effects of environmental influences on the fans and determine whether and how they affect service life. By doing so, we can identify critical points much faster than in the field,” he explains.
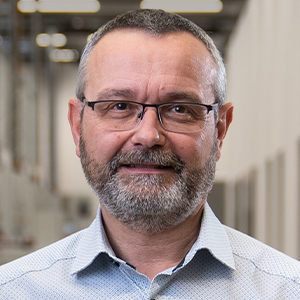
We test fans with real environmental influences and thus for tough use in the field.
Erich Kemmer, Group Leader Validation
The employees of the testing center therefore do not work with ideal laboratory conditions, but with the real environmental influences the fan will face later when in use. These include different physical or chemical influences such as temperature, humidity, salt water, or vibration – of natural or man-made origin. For example, water acts naturally on a fan due to rainfall and in a man-made manner due to the use of the fan in a washing system – both can affect the service life of the product at the customer’s premises.

After a construction period of 15 months, the testing center in Hollenbach went into operation in the spring of 2023.
In an area of approximately 2,500 square meters, several hundred fans per year are pushed to their limits – and beyond – by 8 highly qualified employees.
Recognizing interactions
Kemmer and his team determine the interactions between fans, their components, and their environment through in-depth investigations before, during, and after the individual test fields. Could rapid temperature changes possibly lead to cracks in the plastic? Can moisture then penetrate through these cracks? The team relies on standardized standard tests as well as on combined load tests developed over the years, which are carried out in large climate chambers.
They test the products in the test fields for shock and vibration, climate, impeller strength, spin and cycle test, IP protection class water, salt spray, and in the three accelerated service life tests H0, H1, and H2. It takes at least half a year for a fan to run through all stations. “We always test during and at the end of product development. After all, the fan is not only expected to rotate and deliver the expected air performance, but also be used without any problems in a wide range of areas around the world,” says Kemmer.
Mr. Kemmer, what happens if a fan does not pass a test?
However, it is not only newly developed products that pass through the testing center – new sizes or individual components such as motors or impellers also have to undergo tests. “This allows us to identify errors during the design stage and, if necessary, start again from the beginning – that’s the whole point,” explains Kemmer.
Exclusive insights into all test fields
Learn more about how ebm-papst puts fans to the test in the individual test fields. Each article with exciting insights, videos and pictures!
Leave a comment