In the testing center in Hollenbach, fans are pushed to their limits and beyond with real-life environmental influences. New products, sizes or components pass through the test stations in a total of six test fields over an area of approximately 2,500 square meters. In this series, we take a closer look at each of these test bays. The third focuses on impellers made of metal and plastic.
In the testing center, ebm-papst not only tests complete fans, but also their individual components, such as impellers. Their durability is investigated in the “Impeller strength, spin and cycle test” bay designed specifically for this purpose. The tests are carried out on new products – during and after development – and when introducing new sizes of existing fan series.
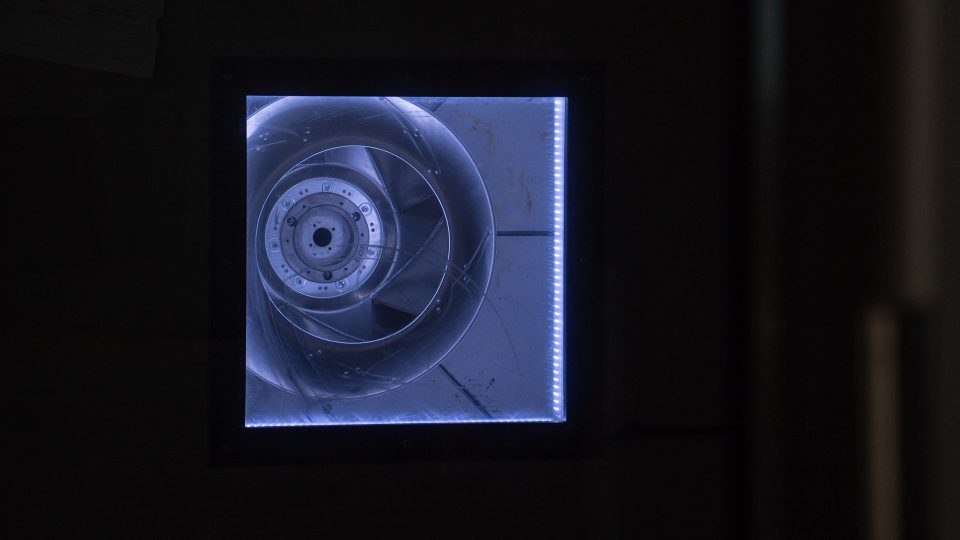
All three impeller tests are ramped-up tests, meaning that the test specimens run at a significantly higher speed than they are later approved for. The load is compressed into a shorter period of time. In this way, the load in the field can be simulated from the speed and duration. Therefore, the engineers identify possible weaknesses very quickly, before the impellers are released to do real work.
Impeller strength test bay
In the impeller strength test bay, plastic impellers are mounted on a total of 11 test benches and operated for 28 days in a row. The focus here is on the special properties of the plastic material: How does it behave over time when centrifugal force and thermal loads act on the fan? After the 28 days, the experts in Hollenbach test the plastic impeller: How strong has the material been? Has the tip gap between the impeller and housing changed thereby? Here, the engineers are guided by standard values and their own experience. This ensures that the efficiency and noise generated by the impeller do not enter a critical range over its operating time.
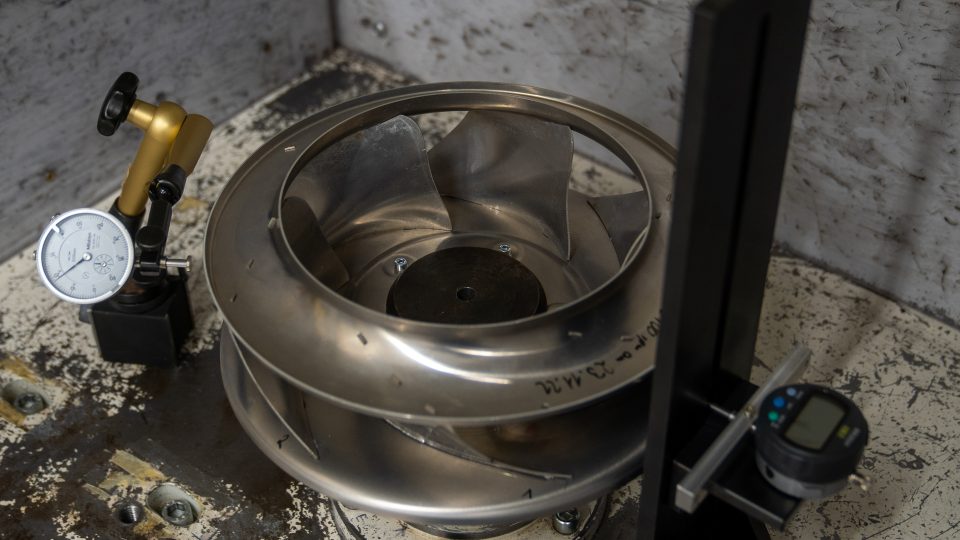
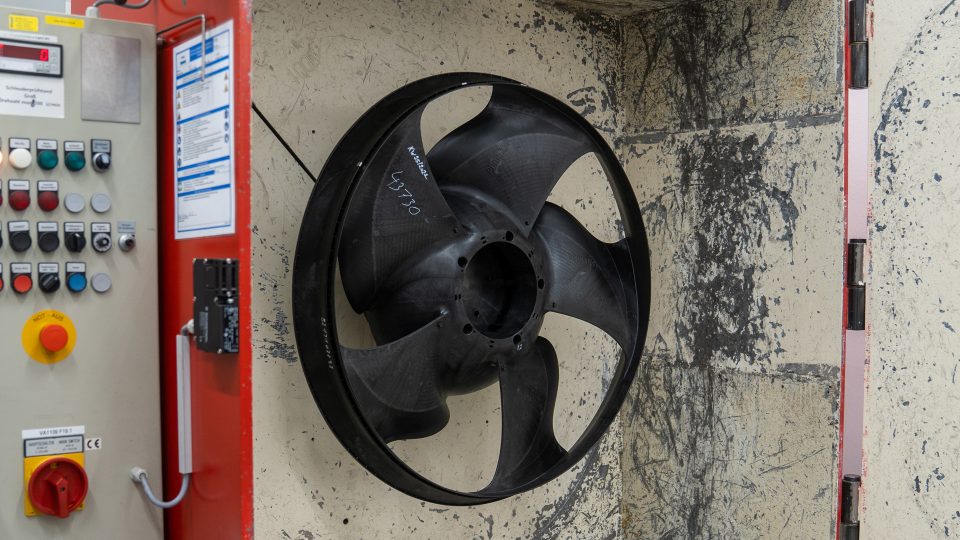
Spin and cycle test bay
The spin test bay features test benches for metal and plastic impellers in different sizes, including for compact fans. Assembled on test benches, this is where the maximum operating speed and the destruction speed are determined, so it can easily come to breaking point here!
The test cabinets continuously carry out start and stop cycles on metal impellers to identify the maximum operating speed and detect potential weaknesses in the material. The test rigs for the cycle test have a drive power of 36 kW and 45 kW, respectively, and can thus run at maximum speeds of 15,000 rpm and 6,500 rpm, respectively. And this with impellers of sizes 450 to 1,250.
Mr. Kemmer, how do the loads on the metal impellers differ?
Exclusive insights into all test fields
Learn more about how ebm-papst puts fans to the test in the individual test fields. Each article with exciting insights, videos and pictures!
Leave a comment