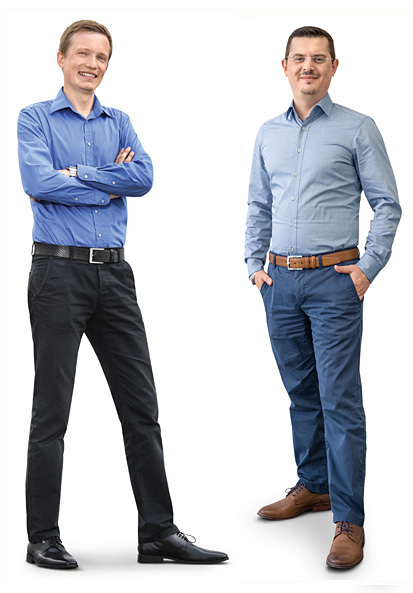
Stefan Magerl (left), Platform Development engineer at ebm-papst Landshut and Remo Fedele (right), Advanced Development engineer at ebm-papst Mulfingen
In die-casting, the molten metal is pressed into a mold at high velocity and under great pressure. The velocity of the molten metal in the gate vg is usually between 30 and 60 m/s. Casting pressures attain values of between 400 and 800 bar. A high mold filling rate and high pressures make it possible to produce castings with high dimensional accuracy and extremely good surface properties. The specific casting pressure occurs in the cavity of the permanent mold. The higher this is, the higher will be the gate velocity.
When calculating the casting pressure it is however important to make allowance for the fact that flow resistances that have to be overcome occur at changes in cross-section and direction, at corners, at edges and on account of wall roughness. These resistances are calculated using a dimensionless quantity, the resistance coefficient φ. According to the Bernoulli equation p=( va2)/(2 φ</span2), a relationship exists between the metal pressure and the gate velocity or flow rate. At low velocity there is a risk of solidification in the gate before the secondary compression of the liquid metal takes effect in the mold cavity. It also results in irregularities in the stream structure, such as slag or oxide particles, and in local clogging. Low flow rates do however cause less turbulence and are favorable with respect to gas removal from the mold cavity.
The local wear and cavitation associated with higher flow rates shorten the service life of the casting mold. These do however normally produce castings with smooth surfaces and a fine-grained structure.
Depending on the casting material and the casting concerned it is therefore important to choose an appropriate specific pressure to obtain a casting of optimum quality. Casting simulation can be helpful here. This numerical simulation is primarily a mathematical description of the Bernoulli equation. It provides a graphical representation of the relationships between pressure and flow rate as a function of the optimum casting temperature for the various alloys. With the results obtained, components and tools can be optimally designed.
Leave a comment