More than half a century ago, the success story of the fan and motor manufacturer ebm-papst began in Mulfingen in Baden-Württemberg. Since then, fan technology has experienced a transformation similar to that of the automotive industry. Whereas then the VW Beetle 1200 with its 38 hp required nine whole liters of gas to drive 100 kilometers, a modern 90 hp Golf requires just 4 liters.
And fans have experienced a similar increase in efficiency – by a factor of six – over the past 50 years. Furthermore, the industry has moved further and further away from selling the fan as an isolated product. Today, manufacturers offer complete functional and assembly modules that can be integrated into a wide range of customer applications without great effort using plug & play. Three phases describe the most important changes in fan technology in the last half century.
Small external rotors as initial ignition
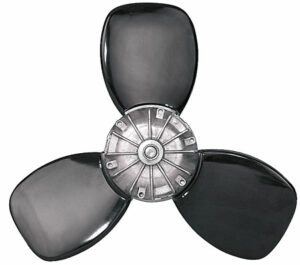
The “Behr fan” – the first external rotor motor that ebm-papst produced and marketed in 1963, still as ebm. (Photo | ebm-papst)
With its establishment in October 1963, ebm-papst played a leading role in the development of fan technology. Gerhard Sturm founded ebm at that time to produce small size 60 motors. This was a new product, as motors of this kind were only available in much larger versions.
Thanks to their design, external rotor motors can be completely lowered in the impeller hub, creating a compact functional unit. The market had been waiting for these small motors: They were soon used in a wide range of applications where space is tight. Applications ranged from range hoods and other household appliances to Schwarzkopf hair dryers.
But the start did not go smoothly: Only three years after it was founded, this motor’s initial problems threatened the company’s very existence. Customers complained about fans that were rattling after just a short time. ebm-papst put all its eggs in one basket and, at the height of the crisis, offered a newly developed motor as a solution to these problems – including a four-year guarantee! How brave this step was is illustrated by the fact that the team had not yet even tested the new product exhaustively.
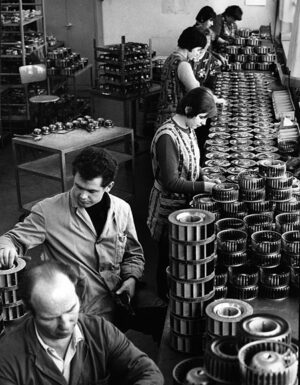
Workers producing centrifugal fans in Mulfingen in 1968. (Photo | ebm-papst)
But the coup was successful – and the new product became an absolute bestseller: the size 68 external rotor asynchronous motor. In the years that followed, ebm-papst derived various other products from this basic motor and continued to develop it. At the same time, the company modernized and automated its production step by step to meet the constantly increasing demand from home and abroad. The courage to keep developing the company was driven by company founder Gerhard Sturm. And his company has taken up the cause: Every product must be ecologically and economically superior to its predecessor.
The areas of application have also expanded greatly since the early seventies: ebm-papst motors and fans are now turning in the computers, air conditioners, oil burners and belt machines of sound studios and they drive agitators in the beverage industry.
Ahead of the curve with the EC motor
However, since asynchronous motor technology had some shortcomings, especially when it came to small motors, in the mid-1970s, ebm-papst started working increasingly on the development of electronically commutated permanent-magnet synchronous motors, so-called EC motors. A rotating magnetic field is generated in these products, which the external rotor fitted with permanent magnets follows. The entire system is significantly more efficient and can be more precisely controlled.
Following its guiding principle, ebm-papst was committed to its new development, even though the prices for the required semiconductors remained high for a long time and electricity costs were relatively low – and so the interest in this energy-saving solution was limited. But the conviction that economic and ecological progress were mutually dependent proved to be correct: At the end of 1990s, the breakthrough for EC motors came in cooperation with a German system manufacturer. Many EC motors are used in its clean room factories.
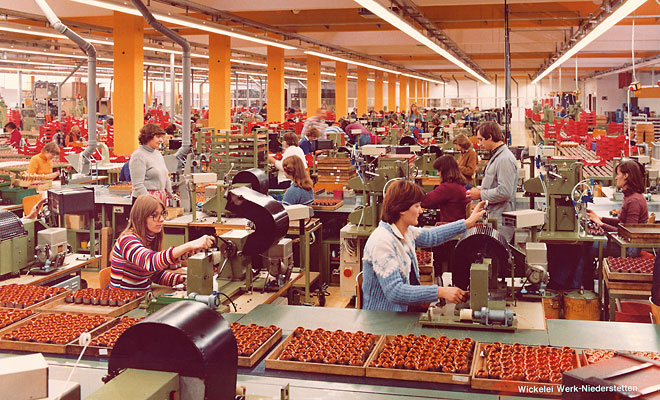
Production at the Niederstetten site began in 1981 with the company’s own winding facility. (Photo | ebm-papst)
At the turn of the 21st century, the EC motors made their final breakthrough. At that time, society and politics were recognizing that the climate can be protected by significantly reduced energy consumption, among other things. As a result, ebm-papst developed EC variants for other and larger products – the largest output today is 12 kilowatts. Gradually, it was possible to increase the efficiency of the EC motors to over 90% in some cases, to significantly increase the power density and thus be easier on the environment.
Two pioneering projects in air conditioning technology at the start of the new century exemplified this trend: A company used the new energy-saving motor in its new generation of air conditioners and a discount chain with locations across Germany used the so-called “EC giants” – EC axial fans with integrated electronics and diameters of 800 to 990 millimeters. This is how customers save not only a lot of energy but also a lot of money in their air conditioners, data centers and household appliances.
More efficient and quieter
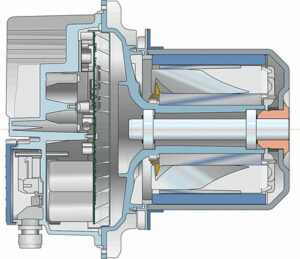
A cutaway model thanks to an external rotor motor featuring EC technology: The rotor does not rotate in, but rather around the stator and works without rare-earth magnets. (Photo | ebm-papst)
The most important developments in the past 15 years have been in the fields of aerodynamics and aeroacoustics. Ten years ago, medium-sized impellers demonstrated efficiency levels between 25% and 45%. These are now in the 60 % range. At the same time, ebm-papst is working constantly to significantly reduce the fans’ noise level, as they are often used in noise-sensitive environments such as hotel rooms or residential ventilation.
With the RadiCal centrifugal fan in scroll housing developed in 2017, the company presented a super-quiet solution for home use. Its aerodynamically optimized housing reduces the noise level by 3.5 dB(A) as compared to a centrifugal blower. If needed, the RadiCal can be combined with the FlowGrid air inlet grille mounted on the intake side. This reduces the turbulence caused by fittings in the unit and, in particular, minimizes disturbing low-frequency sounds.
Getting better and better
In 2010 the “GreenTech” philosophy became the outward manifestation of optimizing products, company processes and production with regard to environmental compatibility. Forward-looking development, environmentally friendly production and maximum energy efficiency are combined with the greatest possible customer benefit. In terms of energy efficiency, this is not yet the end of the story. Even with motor efficiency of 90%, further improvements can be made, for example in terms of aerodynamics.
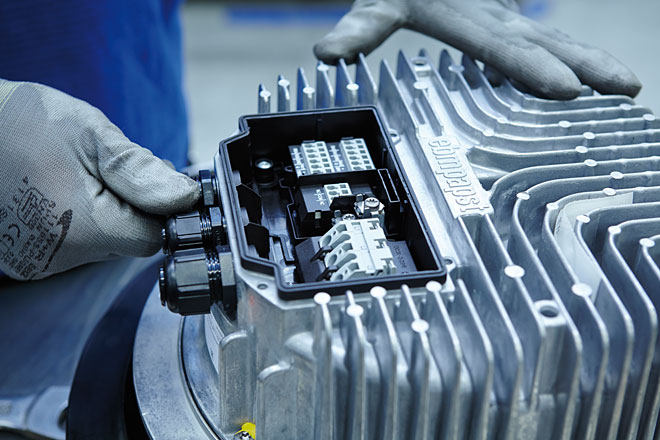
ebm-papst makes products that are ready for Industry 4.0 and interconnects the production processes. (Photo | ebm-papst)
At the same time, ebm-papst is continuing to work to make the production of its products ever more energy and resource-efficient. From a physical and technical point of view, there is still room for innovation here. One of the trends of which the fans are making use is increasing networking under the buzzword “Industry 4.0.” For example, fans can already be integrated completely into system concepts via bus interfaces. This not only transmits the desired speed to the fan, but allows the fan to communicate independently. It therefore reports faults, and also other detailed parameters that can be used to control a building’s air conditioning system more efficiently, for example.
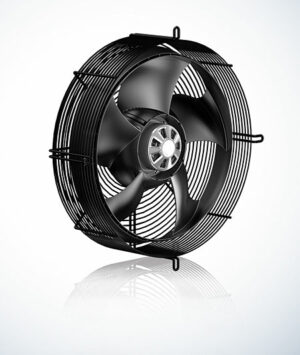
The AxiEco Protect axial fan is used in evaporators, heat pumps and other ventilation and air conditioning devices. Thanks to their very high efficiency, even the AC designs can meet the requirements of the future ErP Directive. (Photo | ebm-papst)
ebm-papst was able to offer solutions for the networked world early on since the electronics were already integrated into its EC fans. And the company is continuing to advance the development of digital solutions: Network-capable air and drive solutions that enable easy remote monitoring and predictive maintenance in addition to focusing on needs. Underlying such devices are intelligent solutions that can collect and transfer data, as well as software that evaluates this data.
But that’s not all: new business models are also required. To continue to inspire the future of fan technology, the company founded the ebm-papst neo start-up in Dortmund in 2017; it is working on the next generation of digital solutions. Meanwhile, ebm-papst has combined its sustainability concept with digitalization: “GreenIntelligence.” This sign is the latest expression of the company’s continuous striving for innovations. And for ebm-papst, this is still the best strategy for successfully shaping fan technology developments in the future.
The most important milestones at a glance:
1963
Establishment of Elektrobau Mulfingen (ebm). In the beginning, the company produced mainly small external rotor asynchronous motors. After their introduction, these compact motors were soon found in various applications where installation space was limited.
1975
Development of the first tubeaxial fan with EC/DC technology. At the time, these were referred to as “brushless DC motors.”
1992
Acquisition of PAPST Motoren GmbH in St. Georgen, Black Forest.
1997
Acquisition of the Landshut site from ALCATEL. The company was renamed Motoren Ventilatoren Landshut GmbH (mvl).
2003
The three companies were renamed ebm-papst Mulfingen, ebm-papst St. Georgen and ebm-papst Landshut.
2010
With GreenTech, ebm-papst implemented a corporate philosophy based on resource efficiency and sustainability. GreenTech encompasses proactive development, environmentally-friendly production, maximum energy efficiency and the greatest possible customer benefits.
2013
ebm-papst celebrates its 50th anniversary.
2016
Presentation of the “AxiBlade” axial fan. It was used in evaporators, condensers and heat exchangers for ventilation, air conditioning and refrigeration technology. ebm-papst achieved revenue of nearly EUR 1.7 billion and employed more than 13,000 people worldwide.
2017
ebm-papst introduced a ready-to-install centrifugal fan for use in residential ventilation units: The RadiCal in a scroll housing.
2018
ebm-papst exceeded the revenue threshold of EUR 2 billion for the first time. This means that growth of EUR 143 million was achieved in this financial year and GreenIntelligence was launched.
2020
The AxiEco Protect axial fan is presented for use in evaporators, heat pumps and other ventilation and air conditioning devices. Thanks to their very high efficiency, even the AC designs can meet the requirements of the future ErP Directive.
Leave a comment