March 2020. Whether you take Bergamo or Strasbourg as an example, in Spring, news about the coronavirus pandemic suddenly made it very clear what can happen when a virus gets out of control, hospitals are overwhelmed and there’s not enough life-saving medical equipment. Employees from Viessmann were also troubled when they heard about the dramatic situation and wanted to act. The company from Allendorf in Northern Hesse began producing face masks and disinfectants in the early stages of the pandemic. Then the staff came up with another idea: why not also produce respirators? After all, a heating system also moves air.
The goal: a respirator that can be deployed quickly
Jan Heiner was pleased to accept the challenge. He is normally responsible for fuel cell heating systems at Viessmann. Starting in March, he led the “respirator” project, which he and 20 other employees were approved to work on. “Of course, we very enthusiastic and we got stuck into the work right away. But we were a bit skeptical about whether it would actually be possible.”
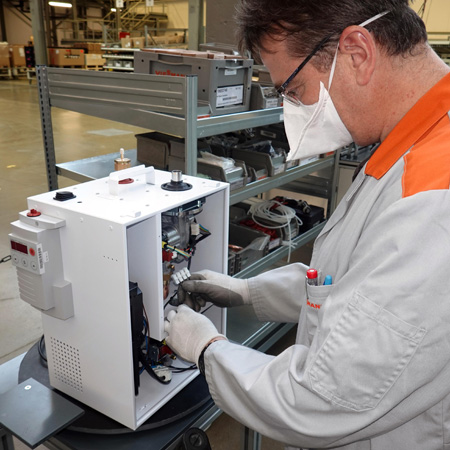
The advantage of Viessmann heating appliances is that they are modular in design. This makes it easy to configure the design. (Photo: Viessmann)
The goal was to have a ready-to-use device as quickly as possible that could save lives. To start with, Heiner contacted anesthetists and intensive care doctors at the Luisen hospital in Aachen, an academic teaching hospital at Aachen University Hospital, to discuss the requirements for this type of device: “The breathing curve is similar to a sine curve. There is an upper and lower pressure level.” For artificial breathing, the device must first build up pressure to allow air to enter the lungs and then reduce pressure so that it can be breathed out. The doctors also pointed out that the oxygen admixture is also an important requirement. “Depending on the course of illness, it’s necessary to supply patients with a higher oxygen concentration,” Heiner explains.
Once he had quickly learned about lung function, he believed that the task was possible. “The advantage is that our heaters have a modular design, so we have the flexibility of replacing components or reconfiguring the structure.” The challenge was then to fulfill the special requirements with existing components. “After all, we didn’t want to interfere with the medical equipment manufacturers’ supply chains, which already had bottlenecks.”
The braking function is the deciding factor
That’s what those responsible at ebm-papst thought as well when Viessmann put in a request for a suitable blower on March 30 in Landshut. Markus Weingart, Head of the Electronics Department, explains: “In St. Georgen, we already produce blowers for these types of applications, but they have to be reserved for medical equipment manufacturers. So we had to look for an alternative that was available right away.” They quickly decided to use an electronic gas blower system that was already produced in high volumes for Viessmann’s condensing boilers. “In principle, the blower doesn’t care whether we mix natural gas and air or oxygen with air, only the gas blower’s very long service life is reduced by the higher oxygen content,” Weingart explains.
In principle, the blower doesn’t care whether we mix natural gas and air or oxygen with air.
Markus Weingart, Head of Department Electronics, ebm-papst
Since a single system solution with an integrated gas valve doesn’t build up the necessary pressure within seconds, the Viessmann engineers decided to connect two blowers in series and take full advantage of the system limits. “Here, it was a great advantage that we knew exactly what the system limits were and didn’t have to take new measurements. We had it all on file. We usually train our products very hard, so we know what’s possible mechanically and electrically, and what the blower can handle,” says Weingart. Nevertheless, a crucial software adaptation was still necessary: a braking function.
This is superfluous in a heater, where the fan impeller simply ends when it is switched off. However, with a respirator, this would be fatal because it would not be possible to breathe out if air continues to flow into the lungs. Therefore, the pressure has to be reduced abruptly. “So, we reprogrammed the brake function. The trick was to make it so that the brake current remains limited. If it’s too high, it could damage components. However, the available hardware doesn’t allow this brake current to be measured, so we had to approach the problem purely theoretically,” says Weingart, describing the challenge they faced.
The tension mounted: Was the unit suitable for use in practice?
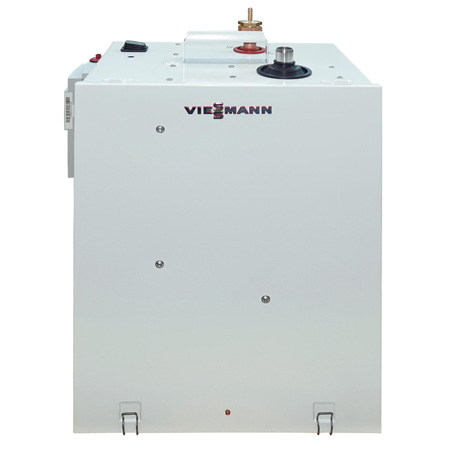
The prototypes are ready and Viessmann is prepared for series production of the respirator.
Just two weeks later, the adapted blower from Viessmann was ready for installation. In the meantime, Heiner and his team adapted the housing, designed the connections for oxygen and respiratory hoses and developed their own air flow sensors. The crucial factor was whether the dynamics fit with the breathing cycle. As it happened, one of the pilots of the Viessmann company jet was also a doctor. When he got wind of the project, he offered his support and provided a breathing dummy for carrying out tests. So far so good, but they hadn’t yet received a decision from specialists in Aachen, who had already received an initial prototype. Heiner and his team were very tense: they had spent many weekends and evenings working. But then came the crucial news: the unit was fundamentally suitable! “We were all really proud, especially as we ourselves were unsure whether we could do it,” says Heiner.
Ready for production for the next wave
Only eight weeks after the project began, Viessmann delivered initial prototype devices to other countries. At the same time, we decided to work together to prepare for mass production of these special blowers so that they would be ready in larger quantities from the summer onwards. “The devices could also be used for mobile use, for example in exhibition halls that are converted into emergency hospitals.”
But things turned out differently: the measures taken to prevent the virus were very effective. Luckily, there were already enough respirators available. “A certified medical device was never our goal. But in the event of a crisis, we would have hoped for a special approval.” Heiner is also glad that the worst-case scenario has not happened so far. Despite this, it has got him thinking: “I’ve seen images from countries where patients have been helped manually with breathing in an operation. Using our devices in these scenarios would have been much better for the patients.”
Leave a comment