The static pressure is a measure of the pressure that the fan can generate in the duct system. This is the pressure required to move air through the system. The total pressure comprises both the static pressure and the dynamic pressure generated by the air movement. As the dynamic pressure is not directly related to the power of the fan system, the total pressure can be misleading in the design process.
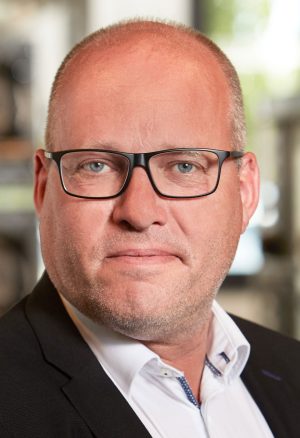
For example, the dynamic pressure with axial fans is generally higher than with centrifugal fans. If you base the system on the total pressure, you may conclude that axial fans have a higher output than centrifugal fans. However, this is not the case if the fans are connected to a duct system. In this case, when designing based on static pressure, the centrifugal fan is usually the best choice.
The static pressure also relates directly to specific energy consumption. That is why it is also the right parameter to use when choosing the fan that will give you optimum energy savings. This is because, once again, the axial fan seems to have a higher efficiency level than the centrifugal fan, measured by the total pressure. However, the centrifugal fan uses less electrical power to achieve the same or an even better result. To assess how much energy is actually consumed to achieve the desired result, it is therefore always best to use the static efficiency.
Total pressure can lead to inaccuracies
Measuring the static pressure is also a relatively simple and straightforward process that can be performed using a variety of instruments. However, the total pressure is more difficult to measure, as the flow rate is measured. In a fan or duct system, finding a measuring point that is not influenced by local speed differences and turbulence, for example, is difficult, leading to inaccuracies in the measurement.
It often takes a lot of experience to correctly interpret measurements containing the dynamic pressure. The situation is different in a measurement laboratory that evaluates fan data, but ultimately it comes down to how energy efficient the fan is where it is actually being used. The static pressure helps to assess this relationship more easily.
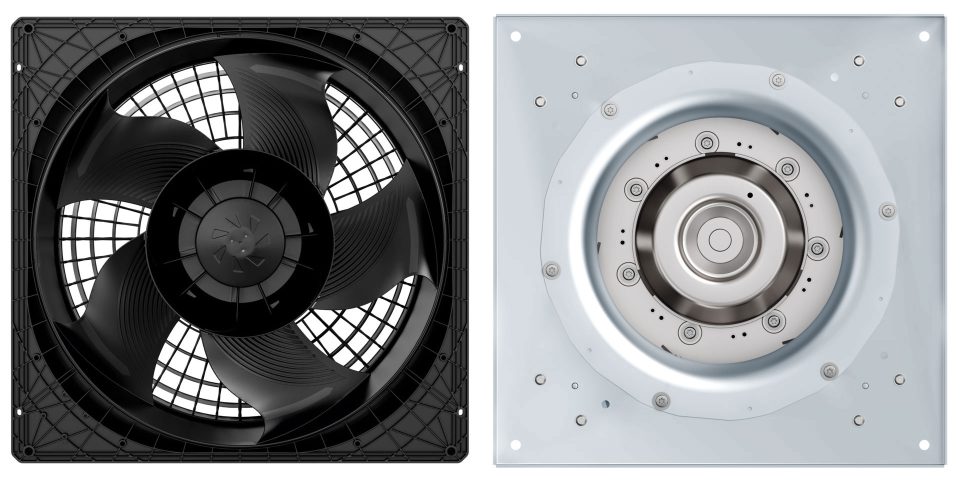
Many fan manufacturers indicate the performance of their products using static pressure, making it easier to compare different models and select the right fan for a particular system and application. Some manufacturers use the overall pressure to advertise their products so that they can indicate supposedly better values. For example, if an axial fan with an efficiency level of over 90 percent is advertised compared to a 60 percent centrifugal fan, this discrepancy may be based on different basic principles.
In this case, the efficiency of the axial fan relates only to the efficiency of the fan impeller based on the total pressure, compared to a complete centrifugal fan, including motor and control, based on static pressure. Comparisons are also made between two complete fan systems, with the axial based on the total pressure and centrifugal based on static pressure. The axial system is given here with a 20 percent higher efficiency level. The difference between the efficiency levels of the two fans is not objective, but rather a marketing method.
Some manufacturers use the overall pressure to advertise their products so that they can indicate supposedly better values.
Axial fans can operate at the same efficiency levels as centrifugal fans. However, it is clear that the laboratory data for axial fans is often difficult to reproduce in practice, as they are more sensitive to disturbances in the installation space than centrifugal fans. This can result, for example, in efficiency losses when converting existing ventilation systems to new energy-saving axial fans. Here, centrifugal fans are less sensitive and can reproduce the data ascertained in the laboratory more effectively, even in real-life operation.
Static pressure is the more suitable measure
In summary, although the total pressure is an important measure of flow dynamics, the static pressure is the more suitable measure for analyzing and comparing fan systems. It is more relevant and easier to measure for the performance of the fan system in a real-world scenario and is often used by manufacturers as a measure of fan performance.
I do not agree with the statement that the static pressure is more suitable. It might be correct when comparing axial and radial fans, but not everywhere else. For example, when a radial fan is ducted, the dynamic pressure at the outlet of the fan is not a loss, and in this case it is more meaningful to work with the total pressure. Using the static pressure in this case leads to an oversized fan. If the radial fan is not ducted, i. e. open outlet, then the static pressure is more suitable. In other words, selecting between the total and the static pressure depends on the boundary conditions under which the fan should operate.
Thank you for your comment, below please find the answer from our author Torben:
The amount of dynamic pressure that can be recovered in a duct system depends on various factors, including the design of the duct system, the flow conditions, and the presence of any devices or components within the system.
In an ideal situation, with a well-designed duct system and smooth, streamlined ducts, it is possible to recover a significant portion of the dynamic pressure. This can be achieved through careful consideration of factors such as duct size, shape, and routing, as well as the use of devices like diffusers or expansion chambers. By minimizing flow restrictions, avoiding sharp bends or sudden changes in direction, and employing appropriate flow control mechanisms, it is possible to reduce the losses in dynamic pressure.
However, it’s important to note that no duct system can achieve 100% recovery of dynamic pressure. There will always be some level of pressure loss due to factors such as frictional losses along the duct walls, turbulence, and the conversion of dynamic pressure into other forms of energy (e.g., heat). The actual amount of dynamic pressure that can be recovered in a specific duct system will vary depending on the aforementioned factors and the specific application.
To maximize dynamic pressure recovery, engineers and designers often employ computational fluid dynamics (CFD) simulations or conduct experimental tests to optimize the duct system’s configuration. These techniques help identify areas of high pressure losses and enable the implementation of design improvements to enhance overall efficiency.
Determining the average percentage of dynamic pressure recovery in a duct system is challenging, as it depends on numerous factors specific to the system and its application. Recovery efficiencies can vary significantly depending on the design, operating conditions, and the intended purpose of the duct system.
In practice, the percentage of dynamic pressure recovery can range from a few percent to over 90%, but it is important to note that achieving extremely high recovery efficiencies is rare. In most cases, a recovery efficiency of around 10-20% or lower is considered typical for duct systems without specialized components or devices.
To achieve higher recovery efficiencies, engineers employ various techniques and components such as diffusers, expansion chambers, and flow control devices. These elements help to minimize pressure losses, optimize airflow, and increase the potential for pressure recovery. However, the actual recovery percentage will still depend on the specific design choices and trade-offs made during the system’s development.
It’s worth mentioning that the term “recovery” is often used in different contexts, such as heat recovery or energy recovery, where the focus is on capturing and utilizing waste heat or energy rather than specifically targeting dynamic pressure. Thus, the recovery percentage can vary significantly depending on the particular objective and the nature of the system being considered. Recovering dynamic pressure means changing it to static pressure or vice versa. These changes are always involving losses.
To sum up the static pressure still accounts for the major parameter when comparing fans. For example, an axial fan can be said to have 20% higher efficiency than the radial fan because the dynamic pressure constitutes that extra part. Now if these 20% are recovered with an efficiency of 10% the extra efficiency of the axial fan when considering static pressure incl. the recovered dynamic pressure will be only 2%.
As the radial fan also has a dynamic component, however smaller than the axial fan we will also see a recovery in this system so the efficiency of the radial fan incl. the recovered dynamic pressure will also be higher – in real life if we include dynamic pressure we bring in a component of evaluating efficiency that is volatile between systems and should be avoided.
If you want to have an example you can use our axial fan with and without the AxiTop: The AxiTop does exactly what I described – change the dynamic into static and increase efficiency – you can also see that it takes a great deal of engineering and components to achieve something here – this is not often done in the market.
Best regards, Torben
As far I understand, fan total pressure should always be the correct baseline for fan selection and comparison. If the actual installation is not ideal, both the static pressure and total pressure are reduced due to installation losses, making direct comparisons to stated pressures doubtful.
The static pressure rise measured on site (and in lab) is affected by the flow velocity at inlet and outlet sides basing on Bernoulli’s principle. If the inlet and outlet areas are not equal, the difference in respective dynamic pressures should be taken into account when comparing the measured pressured to the stated total or static fan pressure.
It is problematic that fan manufactures often do not clearly indicate how the static or total fan pressures they state are defined, and what is the reference installation type for each fan (ducted or not). Moreover, there is constant confusion between measured static pressure rise and “Fan static pressure” which is defined in ISO 5801 as “difference between *static* pressure at the fan outlet and the *total* pressure at the fan inlet”, which can not be measured directly.
In any case, it is crucial that the stated total pressure is the actual pressure achieved in given setup, and not (wrongly) defined as a sum of the measured static pressure rise + the calculated dynamic pressure at fan outlet.
Best Regards, Petteri