Kest Technology produces aseptic mixers for the biotechnology and pharmaceutical industries and is very familiar with pharmaceutical manufacturing requirements. “Our mixers are used to manufacture highly sensitive medicines, some of which are worth several billion dollars,” explains Anders Elliot, Marketing Manager at Kest Technology. That is why the company wanted high-performance electric motors for its new generation of mixers, making it possible to operate even compact models reliably and efficiently. The synchronous AC motors that were previously used could no longer meet these requirements and were therefore replaced with compact, electronically commutated and brushless motors from ebm-papst.
The motors from ebm-papst make our mixers more efficient.
Anders Elliot, Marketing-Manager at Kest Technology
Precise control ‒ up to 80 percent less energy
As the mixers are often in operation around the clock, it was especially important to find an energy-efficient solution. The motors offer a high degree of efficiency across a wide speed and torque range. “We have been working with ebm-papst for about ten years,” says Elliot. “When we were looking for drives, many suppliers were unable to satisfy our energy efficiency requirements for the motors. That is why, in 2017, the product from ebm-papst was chosen for this project.” Jörgen Blomqvist is OEM Business Developer at ebm-papst in Sweden and works with Kest Technology on the project. He explains: “The previous AC motor was much larger and used a lot more energy. By comparison, the smaller EC motors use as much as 80 percent less energy and deliver efficiency of up to 90 percent.”
80%
energy saving
90%
deliver efficiency
Three different sizes of motor from ebm-papst are used in the mixers. The large mixer is equipped with an ECI 80 internal rotor motor and K1 electronics module, combined with an external K4 controller. VDC 49.15 external rotor motors with integrated K4 electronics are used in the medium and small mixers, making them easy to control digitally. “The motors from ebm-papst are inherently smart,” says Blomqvist.
Their speed is now easy to control thanks to integrated electronics and sensors. As EC motors are operated with direct current, the rotational speed can be varied by applying an external signal voltage. There is no longer any need for an external variable frequency drive, as is required for AC motors. This not only saves space but greatly facilitates actuation. Depending on the medicine being manufactured, operators can adjust the speed flexibly and also benefit from the many other options offered by the ebm-papst K4 controller. “This control precision is very important for our customers,” says Elliot.
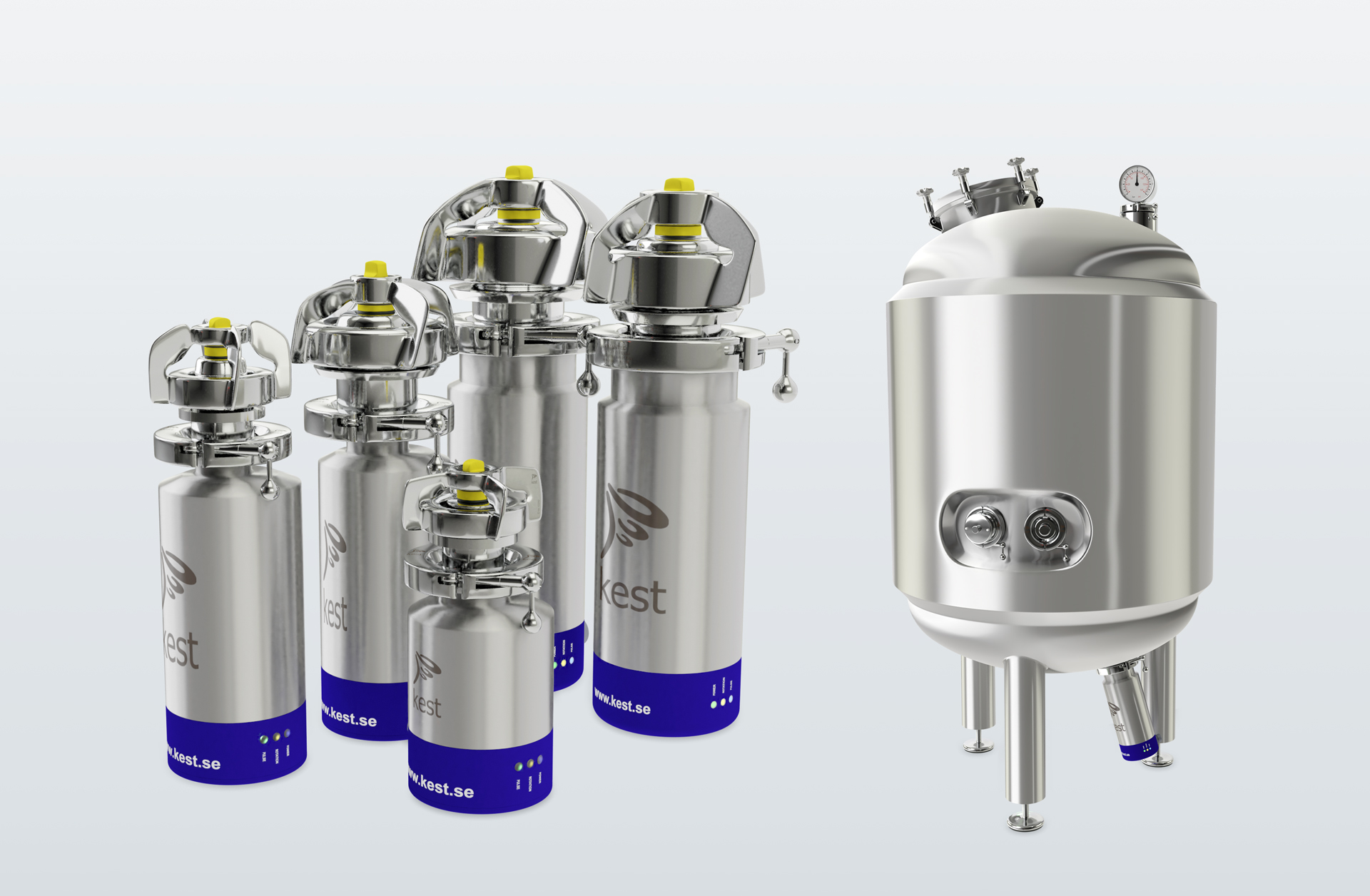
(Image | Kest Technology)
Brushless magnetic drive
In the AC motors that were previously used, the magnetic field was reversed using mechanical brushes. These generate friction when they rotate, resulting in substantial energy loss in the form of heat. In EC motors, the polarity is reversed by an electronic controller that does not produce any frictional heat. This means that no additional fan is needed to cool the mixers. “The fanless drive unit is ideal for the pharmaceutical industry in particular because there are no fans to disturb the clean environment and sensitive air flow,” says Elliot. The EC motors are also much quieter than their predecessors. In clean room workstations in particular, optimizing the noise properties of equipment is important to enable employees working close by to concentrate to the full. Thanks to their NoiselessPlus gears, the VDC motors are particularly quiet.
The efficient motor has many positive side effects for the mixer. We can dispense with the cooling systems that are otherwise needed for AC motors.
Anders Elliot
Compact design
The ebm-papst EC motors are far more compact than the AC motors that were previously used. However, the smaller space made designing the electronics a challenge. “We have a separate control unit, which is not ideal. One cable is for the signal and one for the power” explains Elliot. “Because of laboratory cleanliness requirements, we wanted just one cable between the motor and the control unit.” Working closely with the ebm-papst team in Sweden and Germany, Kest Technology found the solution to this technical challenge. “We had fantastic support from our partner at ebm-papst,” says Elliot. “His technical expertise is very important because he understands just what we need.” The ECI motors ensure the safe and reliable operation of the mixers and satisfy the stringent EMC requirements for electrical appliances in medical applications.
The advantages of ebm-papst motors at a glance
- The mixers equipped with ebm-papst motors can handle up to 1,200 liters.
- Energy consumption is reduced by up to 80 percent.
- The new motors can be controlled more easily and precisely.
- No variable frequency drive is required.
Leave a comment