Quark, yogurt and vinaigrettes line Joachim Müller’s path as he walks through the high-bay warehouse of Elsdorfer Molkerei und Feinkost GmbH, located 70 kilometers southwest of Hamburg. The building was constructed in 2011, and stores the company’s finished dairy products on an impressive 4,500 pallets at a constant temperature of 5 degrees Celsius. Müller is the technical director there. “We store perishable goods here. That means that operational reliability is very important to us. The warehouse must always be kept at a suitable temperature, and there must not be any major failures,” he says.
Room for improvement?
The previous ventilation system completed this task reliably. Four large, direct drive fans each generated an air flow of 62,500 m3/h while consuming 23 kW in power. This meant that the 1,000-square-meter building was always at a suitable temperature. But at the beginning of this year, the energy management system was due for certification according to DIN EN ISO 50001. The energy team at Elsdorfer is always looking out for the potential for savings, but the ventilation system was a sticking point for them. “Of course, the system is a major consumer, as it runs throughout the entire year.
The fans run for 24 hours, seven days a week,” says Müller. But at first, the parties involved were skeptical as to whether replacing the fans would actually bring about the desired energy savings. “The system was only nine years old, we couldn’t imagine that the technology had developed so much in that time frame,” says the technical director.
From one to four
However, the company decided to try it out. After a consultation with Dieter Hildebrandt from Breuell & Hilgenfeldt GmbH, the decision was made to replace one of the four fans first. Müller recalls: “To begin with, we wanted to see whether we could actually make the anticipated energy savings. For reasons of operational reliability, we can only ever convert one ventilation component at a time anyway, as the high-bay warehouse still has to be cooled in the meantime.” With the aims of maximizing reliability, improving air performance, and reducing the noise level, Dieter and his team developed a FanGrid-based concept. This means that multiple fans are screwed into one wall. In the case of Elsdorfer Molkerei, four RadiPac EC centrifugal fans were to replace the first of the four large fans.
To manage this, it required some help from another large vehicle first. Dieter reports: “We used a 40-meter-long, 110-ton car crane to shift the first of the large old fans, which were stored outside the warehouse in system containers.” Compared with that, installing the FanGrid was much easier. The convenient size of the fan cubes meant that two installers were able to bring them into the container and screw them to a wall. They were also quick to connect to the system thanks to plug and play. This was an obvious advantage. After five days of removal and installation work, the FanGrid entered into service, boasting a power consumption of 17.8 kW, an air flow rate of up to 75,000 m³/h, and a maximum pressure build-up of 900 Pa.
“As four fans now work together in one unit, we have improved our operational reliability. If one fails, the other three will take over and keep the air volume constant.”
Joachim Müller, Technical Director at Elsdorfer Molkerei und Feinkost GmbH
A worthwhile investment
After the first fan had been in use for three months, one thing became clear to Joachim Müller and the team: the investment was worthwhile. Elsdorfer saved around 10,000 euros in energy costs, just by replacing the first fan. “We were honestly surprised that we could save that much energy as a result. We weren’t expecting that,” says Müller.
The FanGrid provided other benefits alongside its energy costs: “As four fans now work together in one unit, we have improved our operational reliability. Thanks to the redundant design, it won’t matter if one fails, as the other three will take over and keep the air volume constant,” explains Müller. This is the key point for a warehouse with pallets full of perishable goods.
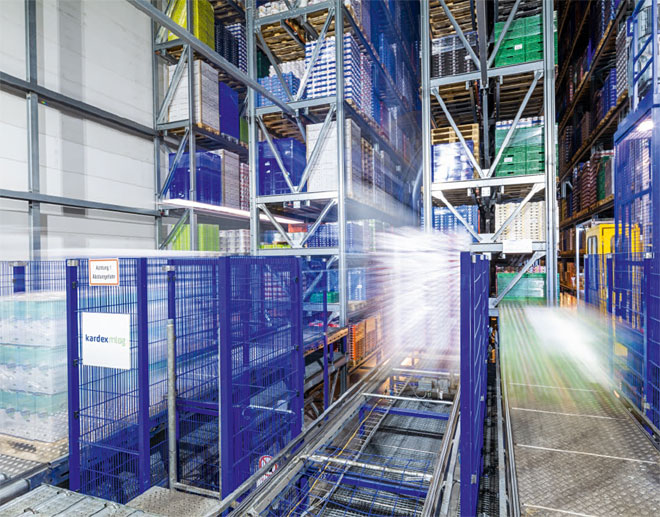
For a warehouse with pallets full of perishable goods, operational safety is a key issue. (Photo: Jan Hosan | Fotogloria)
He also notes the advantages when performing repairs on the ventilation system. It will not be essential to carry them out quickly. In fact, the repair personnel can take their time. Another positive side effect is also a lower noise level. The replacement has decreased this by around 12 dB(A): “We are located in a mixed area, with businesses alongside residential properties. So noise emission is also important here,” says Müller. “And since the project went so smoothly and simply, we agreed that we should also replace the other three ventilation units with FanGrids.”
The four fan walls, made up of a total of 16 RadiPac EC centrifugal fans, have now been in operation since May 2020, keeping the yogurt, quark and other products cool as per requirements. While the old fans required a power output of 78 percent, the FanGrids achieve the same air flow at 50 percent. As a result, Elsdorfer makes two sets of savings – around 47,000 euros per year in energy costs, and 100 metric tons in CO2 emissions.
Leave a comment