The fans used in refrigerated display cases and bottle coolers in the commercial food sector have very long operating times; and so they offer great potential for saving energy. Thanks to their high efficiency levels, EC fans have set new standards in this field. Versions conforming to the European standard EN 60335-2-89 are even suitable for applications involving the use of flammable refrigerants such as R290 (propane), which can form explosive mixtures with air in the event of malfunctioning. What’s more, their intelligent networking capability simplifies servicing and maintenance. Fans have become indispensable features of supermarkets, as the compact refrigerated cabinets for medium and low temperature refrigeration systems could not operate without them. On the one hand the fans ensure that the air circulates around the device, thus keeping all the stored products equally cool. In plug-in refrigerated cabinets they are also used to dissipate heat to the surroundings, or to the central condenser in the case of so-called remote systems. Up until a few years ago, shaded-pole motors were the standard method of driving the fans. There were good reasons for this: Such motors are cheap to make, robust and long-lasting. Their low level of efficiency of just about 20% however means that they are no longer acceptable these days. They have a high current consumption and also produce waste heat that has to be dissipated from the refrigerated cabinet. And so the use of shaded-pole motors is now generally restricted to just a few niche applications.
The energy-saving solution: EC motors as the driving force
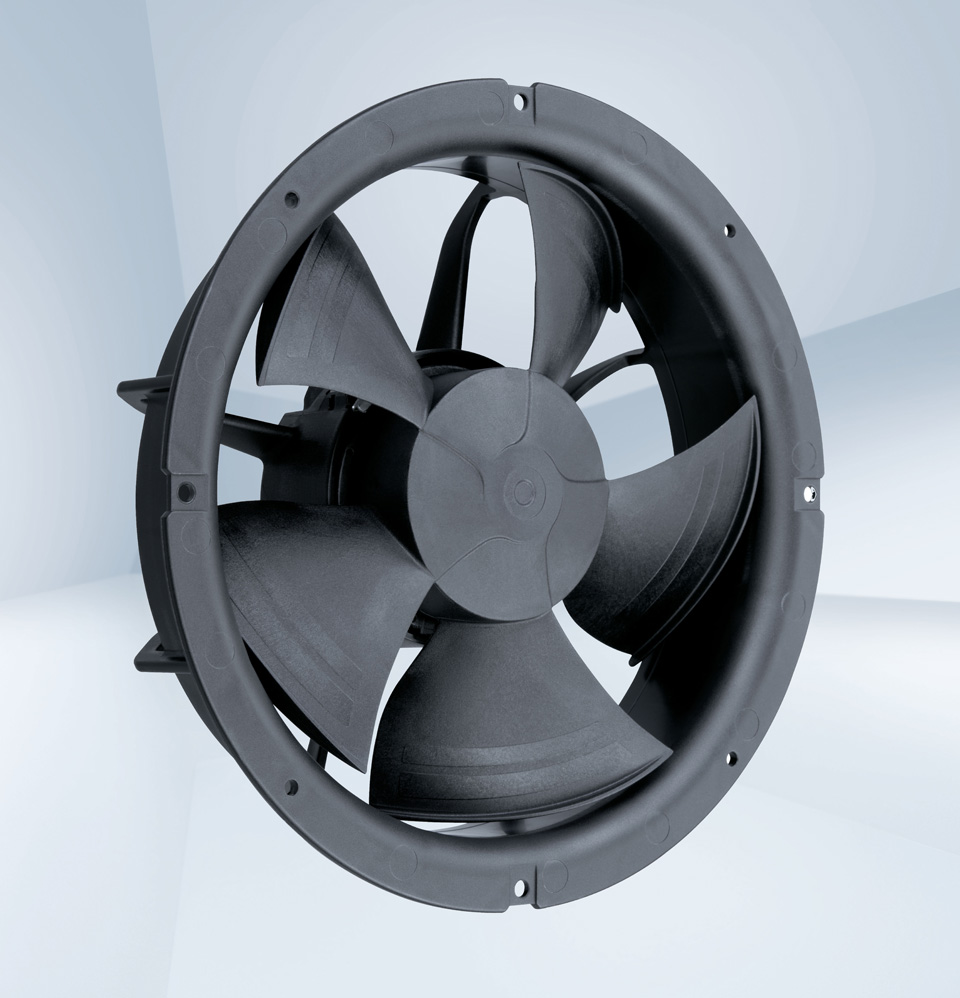
Picture 1: Operating with an efficiency of more than 70%, the power consumption of the ESM motor is only a third of that of a comparable shaded-pole motor and it offers the option of demand-based speed control.
Instead, modern fan concepts are based on the far more efficient electronically commutated EC motor, requiring roughly 70% less energy than the old motor design. As motor and fan specialist, ebm-papst has several such energy-efficient motor versions in its range that are positively predestined to be used as fan drives in refrigerated cabinets: More than ten years ago, the energy-saving motor – known as ESM – was already setting new standards in fan technology for refrigeration applications (picture 1). Operating with an efficiency of up to 70%, its power consumption is only a third of that of a comparable shaded-pole motor and it also offers the option of demand-based speed control. The lower power loss of the EC motor saves yet more energy in refrigerated cabinets. It has a design service life of more than 40,000 hours, corresponding to approx. 5 years in continuous operation. The compact EC motors are available both as OEM components for combination with a separate impeller and as complete plug & play systems with perfectly matching individual components. The axial product range with sizes of 130, 154, 172, 200, 230, 250 and 300 is intended for installation beneath the shelves of refrigerated and freezer cabinets. By contrast, the fans with diagonal impeller of sizes 200 and 250 were designed specifically for installation in the back wall of refrigerated display cases, where installation space is often at a premium (picture 2). Thanks to their extremely shallow design, these fans fit in confined spaces and the diagonal fan design makes them well equipped to deal with the higher back pressure encountered in such situations. Tangential blowers, which likewise operate with EC motors and circulate the cold air in the form of an air curtain, have also been successfully used as efficient solutions for refrigerated cabinet applications for many years now. These are particularly space-saving and quiet-running (picture 3).
Even retrofitting older refrigeration units can be worthwhile in terms of the energy savings that can be realized. For this case, ebm-papst has developed the EC motor iQ-one (Fig. 4). With its motor efficiency of 50%, it is extremely energy-efficient compared to Q motors. It also operates extremely quietly even at full power and is durable. It is mechanically compatible with existing shaded-pole motors and, thanks to identical installation dimensions, enables simple 1:1 replacement up to 5 watts output power. The iQ-one can be combined with the various aerodynamically optimized impellers with 154, 172, 200, 230 and 254 mm.
Reliability: Keeping a constant watch on the fans
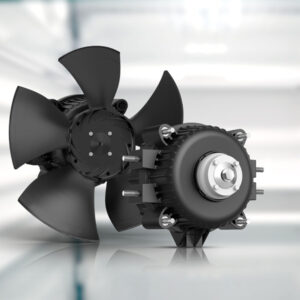
Picture 4: The power-saving iQ-one is mechanically compatible with all Q motors and shaded-pole motors and enables simple 1:1 replacement. (Photo | ebm-papst)
Alongside the lowest possible energy consumption, reliability is another important aspect with regard to refrigerated cabinets in supermarkets. The 1.25 m long standard elements are normally fitted with one to two fans. If a fan fails, it is important to localize and rectify the fault quickly without any adverse effect on the cooling chain and before any food perishes. Preventive maintenance and fan monitoring are also useful.
Here, the networking via the serial interface for communication via MODBUS-RTU helps with the ESM motors. It permits the implementation of numerous surveillance, control and regulation functions in real time by way of remote monitoring. For instance, it is possible to monitor motor operating times with regard to preventive maintenance and to simply localize the fan concerned when service work is needed. Networking via the MODBUS-RTU communication protocol also permits rapid adaptation to changes in operating conditions, for example the cooling temperature can be attained more quickly after defrosting cycles by increasing the fan speed.
Does it really always have to be ATEX?
A further major issue with regard to refrigerated cabinets is the refrigerant used. Modern refrigerants must be safe for the environment and have a low global warming potential, whilst at the same time providing good refrigeration performance. Since January 1, 2015 this has been regulated by the directive (EU) 517/2014, also known as the fluorinated gas directive. Alongside ammonia and CO2, natural refrigerants such as isobutane, propane and propene are thus becoming increasingly popular as an ecological alternative to (partially) halogenated refrigerants. In the event of malfunctioning, the non-toxic hydrocarbons can however form readily explosive mixtures with air.
Regulation (EU) 517/2014 on fluorinated greenhouse gases
Directive (EU) no. 517/2014 on fluorinated greenhouse gases, also known as the fluorinated gas directive, has been in force since January 1, 2015.
Motors and complete systems from ebm-papst are made to satisfy the requirements of the European standards EN 60335-2-24-and EN 60335-2-89 (household appliance standard) and so can safely be used for cooling applications in this sector. This is fully adequate for most refrigerated display cases, as their cooling circuits work with the maximum filling quantities in accordance with the standard (currently 150g A3 refrigerant). Using ATEX components makes no commercial sense in such cases. It is also not sufficient to just use a motor with an ATEX label. The entire fan must have the appropriate approval and the operator has to define an explosion hazard area. The latter is often particularly difficult to implement in supermarkets.
Leave a comment