“In vertical farming, a controlled, climate-controlled environment provides ideal growing conditions,” explains Rudy van den Berg, responsible for marketing and communication at Artechno Growsystems in Maasdijk. “We are focusing on the development of innovative cells.” These are closed chambers of different sizes in which plants grow all year round. Instead of sunlight, these plants thrive in the light of LED lamps – at the perfect temperature and with a balanced humidity and water supply. “Every little plant gets exactly the same attention, can grow perfectly and produce reliable yields.” Artechno mainly wants to reach innovative farmers who are open to this new type of cultivation.

Every little plant gets exactly the same attention, can grow perfectly and produce reliable yields.
Rudy van den Berg, Artechno Growsystems
Not only is the sustenance of the plants almost completely automated, but also the cultivation process. For farmers, the advantage of this is that they save on labor costs. It also ensures that the plants grow undisturbed, as there is no need for humans to get involved at all and no contamination is introduced into the sensitive system. The cells invented by Artechno have a modular design, which offers customers many advantages.
“They can adapt our cells to the needs of the particular crop, the available space and the desired production volume. They start with a few key components, for example, and can expand the vertical farm as required,” explains Rudy van den Berg.
From small cell to factory

The smallest cell that Artechno offers is only 15 square meters in size, meaning that it fits into virtually any barn. If farmers want to grow more plants and increase their yields, they can line up several cells. If they add conveyor belts, washing stations and packaging lines, they have a “plant factory”.
From seedling to delivery, all the processes are automated. This makes a cultivation area of 9,600 square meters or more possible. The cells have automated climate control systems for temperature, CO2, humidity and air flow. In addition, they provide irrigation and supply the plants with nutrients. The light can also be controlled, depending on the desired spectrum and intensity. As an option, the growth of the greenery can also be monitored using cameras as optical sensors.
Vertical agriculture as an industry
Aiming high in vertical farming
Efficient ventilation, air conditioning and automation with fans, blowers, drives and AGVs from ebm-papst.
Rudy van den Berg also refers to Artechno’s cells as plant factories: “It sounds very industrial, but more importantly it makes it clear that the entire process happens in one place,” he says.
“Preferably at a location close to distribution centers, from where the harvested plants can then be brought directly to the supermarkets. In terms of logistics, you save a lot of time and mileage compared to a field harvest.” According to Artechno, almost all crops are suitable for vertical cultivation, especially lettuce, herbs, seedlings and berries.
“The land or region where the cells will be located often determines what is profitable for the farmer. You can often achieve a better and more consistent price in places where traditional cultivation of the crop is difficult, for example.”
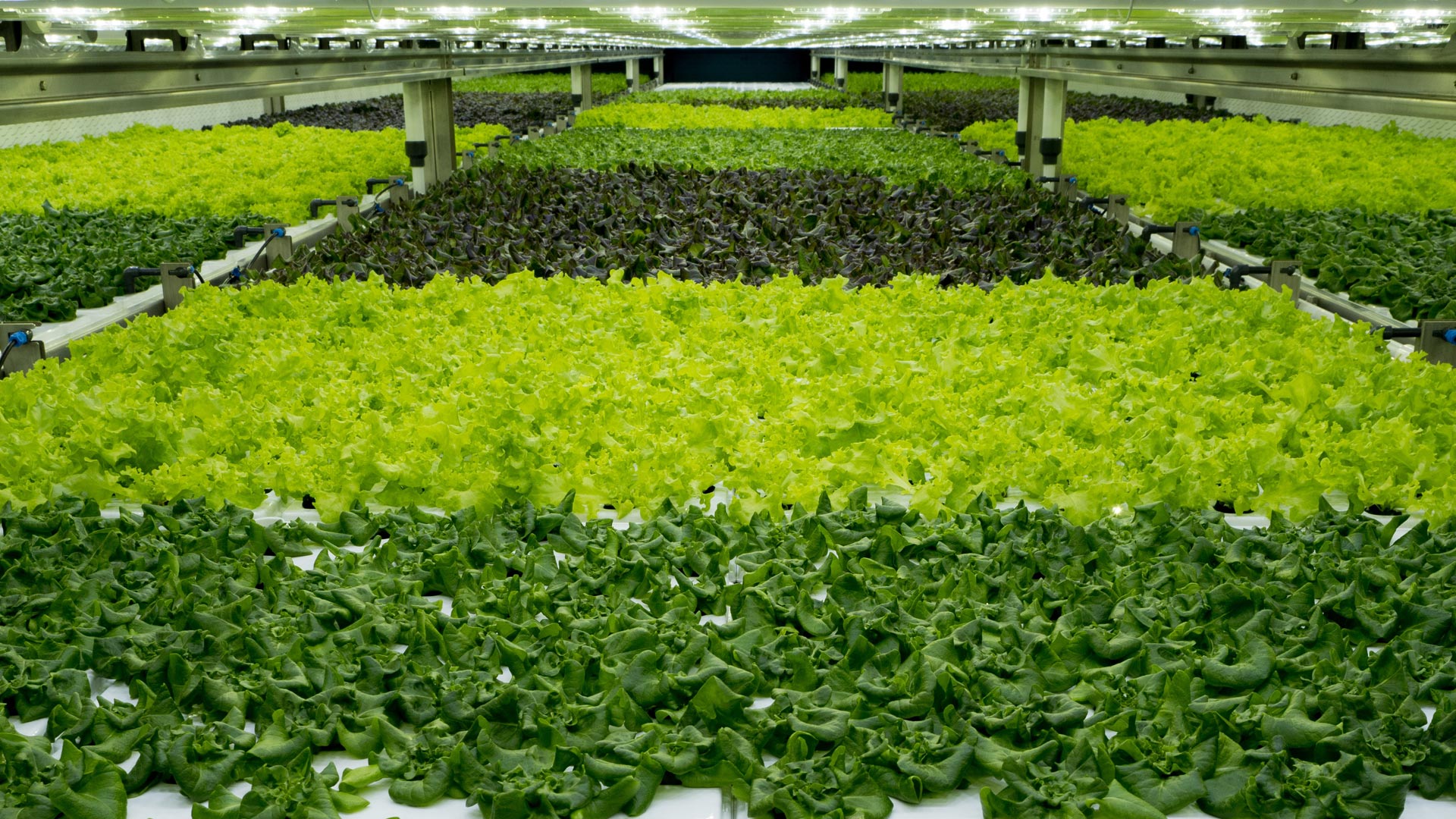
Optimum growing climate with the RadiPac
The growing climate naturally plays a crucial role in the cells developed by Artechno. Perfect ventilation is crucial for growth – and it was moving air that brought the company into contact with ebm-papst. Rick van Oosterom, sales representative at ebm-papst Benelux, explains: “In October 2020, we made contact – we presented our range of motors and fans to Artechno.
It turned out that they were buying a ready-made ventilation unit and installing it in the cells. But they wanted to change that, so we worked together as partners and experts in our respective fields to find a new solution.” ebm-papst Benelux offered an alternative fan that performed significantly better than the previous solution, both in economic and ecological terms. But Artechno was not yet fully convinced.

Instead of three different fan types with different operating points, they wanted to use just one model in the cells that would efficiently cover all three operating points. “That was quite a challenge. Our first choice would have been the AxiEco, but as Artechno controls the air volume via a differential pressure measurement, the only option was a centrifugal fan.” They opted for the new RadiPac C. “It was the perfect solution, both economically and with regard to efficiency. It can keep the air quality in the greenhouse at an optimum level,” explains Rick van Oosterom. Thanks to its EC motor, the fan can continuously adopt different operating points and always works at an efficient optimum.
The Radipac C was the perfect solution, both economically and with regard to efficiency.
Rick van Oosterom, sales representative at ebm-papst Benelux
Now the fans ensure a perfect air flow that allows the plants to grow optimally. Depending on the design, between 12 and 24 fans are installed in the Artechno cell. “Every crop needs a specific microclimate,” explains Rudy van den Berg. “We have to monitor this closely. Mold is always a risk of cultivation, but with a controlled and flexible air flow, we can completely rule it out.”
Leave a comment