The company EVC operates a highly exclusive gas power plant in Dresden. Its only customer is the neighboring microchip factory of Globalfoundries, the semiconductor industry giant. The power plant supplies electricity with an extremely stable voltage and frequency across the way, guaranteeing the chip foundry a worry-free energy package. On site, every day Zeppelin Power Systems makes sure that the systems in the gas plant function perfectly.
Senior Service Technology Engineer Andreas Büttner runs a tight ship there. “We are constantly on the lookout for potential means of getting more with less energy. We take environmental and climate protection very seriously,” said Büttner. “In 2015 and 2016, we updated and equipped the horizontal condenser on the roof for the cooling water with 216 EC fans.” The result was an almost 87 percent savings on energy. “That spurred us on to search for more potential and we found it in the air intake system.”
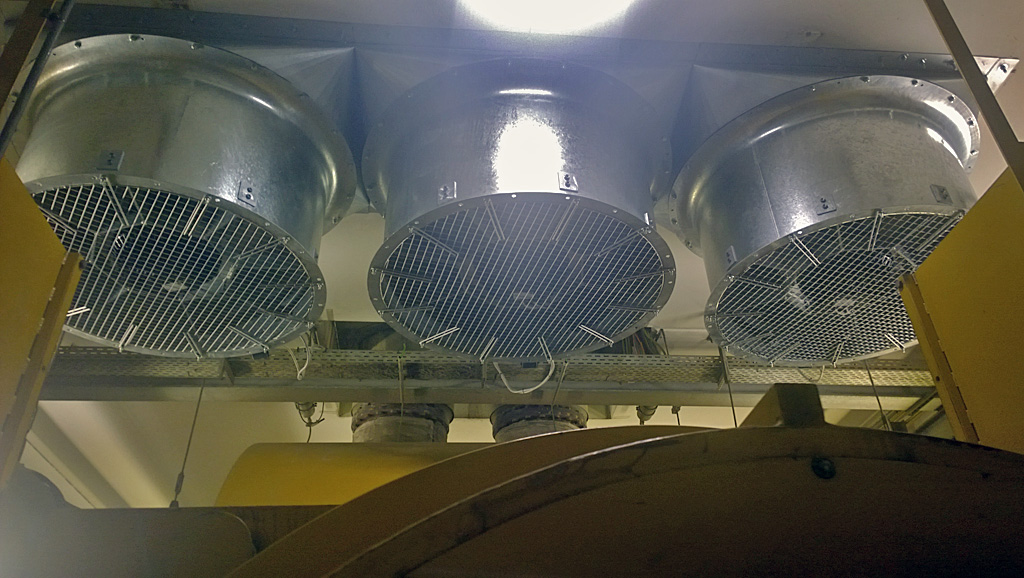
Three medium-pressure EC axial fans now supply the gas engines with combustion air. Their biggest plus in this context: they are easy to maintain. (Photo | ebm-papst)
Less pressure works too
The air intake system supplies the new gas engines with combustion air and cools the space in which they roar and bellow – which happens to be as large as a two-car garage. An air duct leads from each of the new rooms. Today, three EC medium pressure axial fans are mounted on each ceiling and transport air inside. “Until a short time ago, it was one AC centrifugal fan. Unfortunately we didn’t have enough space back then and they were positioned so poorly that half of the fan cross-section was blocked. And the air intake system had ducts that were too narrow. We simply decided to convert everything.”
The advantages are obvious: with three fans we have redundancy. If one fails, the engine can still be operated.
Andreas Büttner, Zeppelin Power Systems
Büttner commissioned an engineering office to completely revise the air intake system. The goal was to significantly reduce the required air pressure at the same air volume. “We enlarged the pipe cross-section, modified the air grid and optimized the shutters – the entire system from beginning to end.” This reduced the required pressure from 560 Pascal to 307. And instead of one large centrifugal fan, Büttner was able to install three medium pressure axial fans to distribute the air. “The advantages were obvious: with three fans we have redundancy. If one fails, the engine can still be operated,” explained Büttner.
“But in my opinion, the biggest plus was that the axial fans now hang from the ceiling. They were easy to install, and maintenance and repair will be much easier too. When we used to have to replace a defective centrifugal fan, it was a big deal: we even needed a crane. Now if worse comes to worse, we just need a three-technician team.”
95 percent energy savings
After running the new system for nine months, Büttner measured the amount of energy that was saved. “It now takes an amazing 95 percent less energy to run the air intake system than before. With the new engines, the system now saves us 1.4 million kilowatt-hours – around 792 tons of carbon per year!”
Leave a comment