Hospitals and laboratories are subject to stringent hygiene requirements. Simply cleaning utensils used in operations, such as scissors, tweezers, clamps, test tubes, and pipettes is not sufficient, because the biggest danger is invisible to the naked eye: bacteria, viruses, or chemical residues can falsify measurement results in laboratories or, in the worst case scenario, can cost human lives. With his work, Ezio Gobbi and his team helps to ensure that this does not happen. For over 30 years, the engineer at Smeg, since 2009 in the manufacturing unit of Bonferraro, has been developing thermal disinfectors. These special washing devices ensure that utensils are perfectly cleaned in hospitals, doctor’s offices, and research facility laboratories.
Bonferraro is based in the community of the same name in the Province of Verona, Italy and is the subsidiary of household appliance manufacturer Smeg. The company has been manufacturing thermal disinfectors since 1987. “There are only around ten manufacturers worldwide that make such devices,” says Gobbi. Most recently, the R&D team was tasked with developing three types of devices with wash chambers ranging from 250 to 450 liters, in other words, high-performance devices that have to operate with maximum reliability. And not only when it comes to cleaning results: “If a dishwasher at home fails for a few days, it is irritating but not disastrous. However, in hospitals or laboratories, work is severely disrupted,” says Gobbi. This means that the technology installed must be 100 percent reliable.
Disinfection in the high-tech dishwasher
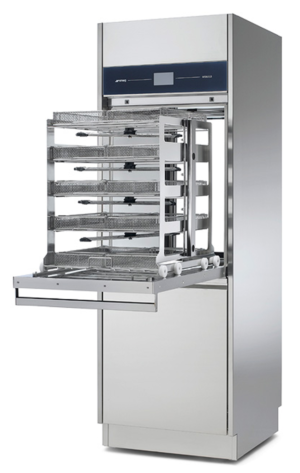
Works like the dishwasher at home – only much more precise: the thermal disinfector from Bonferraro. (Photo | Bonferraro S.p.A.)
A thermal disinfector works in a similar way to a dishwasher at home. There are washing and rinsing phases, and the items are dried at the end of the program. However, there are also major differences. The devices have to work with much greater precision than those in the kitchen at home, and they are subject to the strict requirements of medical products. This even applies to the removal of coarse dirt. “If residue persists, the sterilizer is then unable to completely kill bacteria even at 140 degrees Celsius,” says Gobbi.
This is not so easy, as the objects to be cleaned come in a much greater variety of shapes than pots, dishes, or cutlery in the kitchen at home, for example. Everything gets put in there, from scissors and test tubes to hoses. This is why special carrying systems are required to allow the water to get everywhere. The water supply and the special cleaning chemicals must also be dosed in exact amounts and the temperature must be regulated precisely. Therefore, a thermal disinfector has an additional disinfection phase, during which it is important that the temperature is between 90 and 93 degrees Celsius exactly.
Reliably dry
Drying begins when disinfection is complete: the crucial phase. There must be no droplets of water left on the objects so that they can then be immediately shrink-wrapped and put into the sterilizer. Depending on the shape and material, this process takes between 15 and 30 minutes. “For example, plastic is much harder to dry than glass,” says Gobbi. Here too, the choreography is finely tuned: first, air is blown into the washing chamber at low pressures so that the steam escapes slowly. Then hot air is supplied at different speed levels and at up to 120 degrees Celsius. “We developed a drying cycle here that works as quickly and efficiently as possible,” says Gobbi. The blower is the crucial component for this process. It had to be especially powerful for Gobbi’s three new types of devices, also because it has to cope against the resistance of the HEPA filters. HEPA stands for High Efficient Particulate Air. The filters prevent germs and dust particles from outside entering the washing chamber.
We developed a drying cycle here that works as quickly and efficiently as possible.
Ezio Gobbi, Engineer at Bonferraro
So Gobbi approached ebm-papst: “For me, it was the logical step. We have been working together for more than 30 years on other projects.” Gobbi says the other projects involved usual household dishwashers, which Bonferraro also manufactures. But the blower solutions used for these devices were insufficient for Gobbi’s requirements or would be too large for the available installation space at the required power. And a tailored solution was out of the question: “This is not a mass market like with household dishwashers. We simply do not have high enough quantities of them: it would not pay off. We needed a product that had already been developed.”
A solution from the boiler
Therefore, Fabio Milani, Key Account Manager and Gobbi’s contact at ebm-papst Italy, had to look for a different way, working with the experts in Landshut. “The power requirements described by Gobbi were a pretty good fit for the blowers that we usually use in condensing boilers: the VGR 118 and the VGR 148,” says Milani, adding, “a particular version of VGR 118 had a high-performance motor to make one blower suitable for all three types of devices.” Thanks to EC technology, the blower types enable high speeds and, as a result, high pressures that can overcome the HEPA filter, and all that with a compact design. They are also infinitely adjustable so that the speed can be precisely adapted to the different drying phases. So the perfect solution? Almost, if it were not for the venturi attached to the blowers as standard. In condensing boilers, it is essential for regulating the gas supply. In Bonferraro’s thermal disinfectors, it would just be disruptive.
Out with the standard solution and on to the more expensive customized solution then? Something else happened. Milani explains: “As happens by chance, the same blower was being created at the same time as variants without venturi.” Gobbi benefited from this. He can also use it for his three types of devices. “In addition to the performance characteristics, the geometry was a perfect fit for our requirements,” says Gobbi. The three new thermal disinfectors are under development and the start of production is planned in July 2022. The demand for the Bonferraro devices is growing. “The coronavirus pandemic has led to a significant increase in sensitivity to hygiene. And this has impacted our company,” he concludes.
How a thermal disinfector works: A hospital as an example
During an operation, a surgeon uses numerous instruments: scalpels, scissors, tweezers, and many other different operating utensils. Some are thrown away immediately after use. Others have to be cleaned, disinfected, and sterilized before they return to the operating room.
01 Cleaning begins
In hospitals, the thermal disinfector is located between an unclean room, from which it is loaded, and the cleanroom, where the cleaned instruments are picked up. Therefore, it has two doors. Before loading, a specialist pre-cleans the instruments manually.
02 The washing program
As with a normal household dishwasher, it switches between washing and rinsing phases. However, the processes in a thermal disinfector, such as supplying cleaning chemicals, are controlled much more precisely.
03 Disinfection
Demineralized water is used for the washing process in the disinfection phase. Normal tap water contains too many foreign bodies, such as salts, that could remain on the objects. During disinfection, the temperature must remain constant at 90 to 93 degrees Celsius.
04 Drying
The drying process comes at the end of the program. Bonferraro developed a finely balanced system for this process. There, the blower overcomes the HEPA filter with high pressure.
Depending on the selected program, the entire rinsing program takes between 25 minutes and just under two hours. From the cleanroom side, the disinfected instruments are removed, bagged and then put into the sterilizer. Only then are they ready to be used for the next operation.
Leave a comment