Operating cleanrooms with FFUs is the most economical option to ensure a clean air supply. At the core of these FFUs are compact, modular, built-in fans that are as flat as possible, meaning that they require little installation space, and work with high energy efficiency. However, integrating the systems into a network is also becoming increasingly important. The air supply in a cleanroom is not usually a standalone solution. Instead, it is integrated into the entire automation process and its PLC and SCADA systems. Just like all other sensor and actuator information, the fans of the FFUs have to be integrated into the system network, and their status information must be provided to the controls and visualization systems.

Figure 2: Fans with a MODBUS daisy-chain interface (DCI) can be addressed automatically by the master via a hardware signal. This makes commissioning proceed much more quickly. (Photo | ebm-papst)
The initial commissioning of a cleanroom system requires a significant output of time and money. Based on user reports, the time required to manually connect an FFU data point is around five to ten minutes. The more fans there are in use, the more potential there is to make savings. The fan and motor specialist ebm-papst has responded to this and offers EC centrifugal fans, which are specially designed for installation in FFUs and have a digital MODBUS RTU interface, with automatic addressing, which can significantly reduce commissioning costs (Fig. 2).
MODBUS RTU with automatic addressing
A master/slave-based bus always requires unique slave addresses. The fans are usually delivered with an address that is preset in the factory, which is always the same (e.g. slave ID = 1). Therefore, the addresses must be assigned a unique address during commissioning for operation in the network group, preferably in the order of the MODBUS cabling. This time-intensive process is now automated using “DCI” (daisy-chain interface) addressing.
The master controller is able to manage the complete addressing procedure along with the localization of the FFU devices.
A fan equipped with a DCI is addressed by a hardware signal (15 V/24 VDC) via the Init pin on the RJ45 network plug, and thus temporarily becomes slave address 247. Only the unit activated in this manner “listens” to messages sent to this DCI address 247, and accepts a new MODBUS address sent by the master controller to this slave. Following successful re-addressing of this fan, its DCI relay is switched on and the hardware signal (15 V / 24 VDC) is switched on to the Init pin of the next fan module in the chain. This fan is now activated via the hardware signal (Init pin) and the addressing continues as described above.
If the cable diagram is known, the position of the fan unit in the cleanroom ceiling can be determined using the order of the addresses or the cable route. The installation location can be identified using the order in which the addresses are allocated. Manual assignment is no longer necessary; the master controller is able to manage the complete addressing procedure along with the localization of the FFU devices which are installed in the cleanroom ceiling. There is a significant reduction in the time and costs for commissioning.
Energy-efficient and quiet
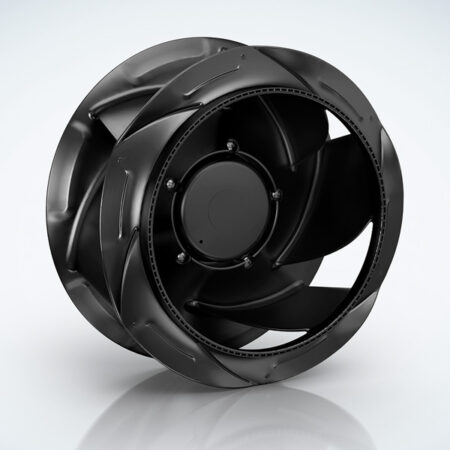
Figure 3: The fans from the RadiCal product range are particularly well-suited for use in filter-fan-units. (Photo | ebm-papst)
Once put into operation, the energy efficiency of the fans becomes an important matter. Nowadays, FFU manufacturers have to guarantee overall efficiency levels of at least 50% in cleanroom applications at the design point. Therefore, there is a great demand not only for fans that are as flat as possible, but also for fans that work energy-efficiently. EC technology therefore has a lot to offer cleanroom technology, as FFUs equipped with it can achieve efficiency levels of well over 50%. EC fans can also be used to meet strict noise emission requirements.
RadiCal centrifugal fans lend themselves particularly well for this purpose (Fig. 3), as their impellers have been optimized according to aerodynamic criteria. They therefore contribute to a significant noise reduction of up to 7 dB(A) compared to the conventional industry standard, which human hearing perceives as half as loud. The quiet and energy-saving fans are available with diameters of 250, 310, 355, and 400 mm, and cover air performance levels in the ranges of 580, 1,170, 1,750, and 2,330 m³/h, with a back pressure of up to 250 to 300 Pa. Thanks to their external rotor design, they are very compact and above all extremely flat, at a height of 190 to 275 mm, meaning that they can be easily integrated into the equally compact FFUs.
Impellers made of plastic composite materials have already been successfully introduced for use in many cleanroom environments, and have proven effective. Nevertheless, ebm-papst has had the relevant materials tested for cleanroom compatibility in an external laboratory. The fans in the RadiCal product range were examined thoroughly for substances that are prohibited in cleanroom operation, and evaluated according to the standards of the semiconductor industry. They passed the corresponding tests with flying colors, as the materials used are harmless, as is the outgassing process. This means that in cleanroom technology too, users can benefit from the energy-saving, innovative design of the plastic impellers. After all, plastic offers a much wider range of design options compared to sheet metal materials. As a result, the design of the whole fan leads to improved air flow through the impeller, which significantly increases aerodynamic efficiency.

Figure 4: The EC fans can be easily integrated into the FFU. They are supplied as ready-to-connect systems, which have been tested at the factory. (Photo | ebm-papst)
Wide voltage input with active PFC
The EC fans can easily be integrated into the FFUs (Fig. 4). They are supplied as ready-to-connect systems that have been tested at the factory, either as EC centrifugal fans with a cable and connector panel, or as fully assembled fan installation modules complete with nozzle plate, motor support plate, profile struts, and guard grill. Thanks to a wide voltage input, they are suitable for international use with a wide variety of line voltages and line frequencies. The standard active PFC (Power Factor Correction) prevents the permissible harmonic limit values from being exceeded during the parallel operation of many EC fans, which would otherwise put a strain on the supply network.
Thanks to a wide voltage input, the EC fans are suitable for international use.
All energy distribution components such as network transformers, fuses, switches, and cable cross-sections can be designed to be much smaller and more cost-effective due to the active PFC. Additional external harmonic filters are not required. But it is not only in large cleanrooms where users are well-served by EC centrifugal fans. ebm-papst also offers suitable components and system technology for FFU operation and monitoring for smaller cleanroom cabins.
Cleanroom technology for air-purifiers
We are currently seeing an emergence of entirely new fields of application for cleanroom technology devices and suppliers that specialize in the prevention and dilution of particle concentrations in rooms. After all, this is precisely what is required for preventing and diluting aerosol concentrations that cause, for example, virus loads in classrooms. This virus load can be reduced through air recirculation using the same filter technology as in cleanrooms. The indoor aerosol concentration is reduced by separating aerosols in the HEPA filter during recirculating air operation. Noise generation is also important to this field of application, as it determines the acceptance of the air purifiers. ebm-papst’s quiet fans and the expertise of cleanroom device manufacturers make practical solutions possible here. After all, it is vital to clean the classrooms so that they are free of particles, thus minimizing the virus load.
Leave a comment