In applications relating to refrigeration, air conditioning and ventilation technology, users frequently observe that the selected fan installed in the device does not run as quietly as expected. Such fans often generate a level of operating noise considerably higher than that stated in the product documentation. The reason for this is simple: the values stated in the documentation are based on reproducible measurements under standard conditions (without any disruptions). However, the applications themselves are subject to inflow disruptions of varying intensity that are caused by the installation conditions in the respective device. These lead to additional noise generation. Help is now at hand thanks to an air inlet grille that essentially has a straightening effect, considerably reducing undesired disruptions and effectively reducing the level of noise generation.
Heat pumps and air conditioners are installed in different ways, with varying dimensions and designs. For example, differences occur in the positioning of the openings required for ventilation, in the heat exchanger surface and in the packing density. The air flow that enters the fan is therefore influenced by the other components such as the heat exchanger, in addition to being influenced by the installation situation. Depending on the application, the inflow to the fan is subsequently highly uneven and contains non-stationary components. For example, the housing walls of rectangular heat exchangers exhibit backflow regions with corresponding circulation – that is, air turbulence (figure 1). These in turn are then directed towards the locations with the least amount of clearance between the fan and the housing wall. It is here that the turbulence from both sides is combined, causing ‘vortexes’ that generate high levels of turbulence. This causes major fluctuations in the pressure and speed at the front edge of the blade, which can sometimes lead to drastically increased levels of additional noise, particularly in the low-frequency range. This generates broadband noise and narrowband, tonal frequency components, also referred to as tonal noise.
The tonal noise consists of the blade-passing noise and its harmonics. The formula for this is f=n*z*k. The frequency of the blade-passing noise f is calculated from the product of the speed of the fan n and the number of blades z. The harmonics of the blade-passing noise are the multiple of this, designated as k. Accordingly, an axial fan with five blades and 1,200 rpm (20 rps), for example, would result in a blade-passing noise at a frequency of 100 Hz. We are all familiar with the unpleasant ‘humming’ noises that are typically generated as a result.
Putting an end to ‘humming’ noises

Figure 2: The air inlet grille drastically reduces the noise-generating disruptions to the inflow and is equally effective with both axial and centrifugal fans. It has virtually no effect on power input and air performance
The additional noises generated by heat exchangers and air conditioners are not only undesired, they are intolerable. This is particularly the case in residential environments, although eliminating these noises is far from easy. It is not possible to compensate for disruptions to the inflow by optimising the fan. Providing additional insulation for the housing also brings little success in practice, as corresponding insulation panels are typically only effective as of higher frequency levels. The fan specialist ebm-papst Mulfingen therefore took a different approach: if you improve the inflow of air to the fan, this reduces the turbulence and therefore also reduces the unpleasant low-frequency noises that are caused by this.
With this in mind, the Mulfingen engineers developed the special FlowGrid air inlet grille which has a straightening effect on the inflowing air (figure 2). This drastically reduces the noise-generating disruptions to the inflow and is equally effective with both axial and centrifugal fans. In the case of a condenser fitted with an axial fan, for example, the deployment of the air inlet grille reduces the noise level by 3.9 dB(A) and the tonal noise by 16 dB. With regard to a low profile air conditioning device (diameter 250 mm), the FlowGrid reduces the noise level by 2.5 dB(A) and reduces the tonal noise by 9 dB. Figure 3 shows the actual results of a noise measurement performed on an example condenser.
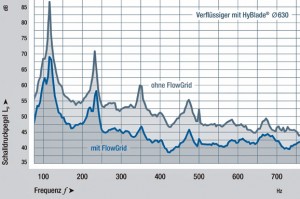
Figure 3: The air inlet grille achieves a significant reduction in the sound pressure level and considerably weakens tonal noise. The figure shows the actual results of a noise measurement performed on a condenser
The use of the air inlet grille reduces the sound pressure level and considerably weakens the tonal noise. Therefore, there is significantly less need for insulation and noise protection. The air inlet grille is made of injection-moulded plastic and satisfies various fire protection classes up to UL94-5VA. You can use screws to quickly and easily secure the FlowGrid to axial and centrifugal fans, and it is possible to implement any necessary application-specific adjustments while securing the FlowGrid. Depending on the design of the end device, it is even possible to retrofit the FlowGrid, for example in the course of any upcoming service work. In the case of a size 800 axial fan, the air inlet grille requires only around an additional 15 cm of installation space in the axial direction, which is typically available in the applications.
A further option for acoustic improvement
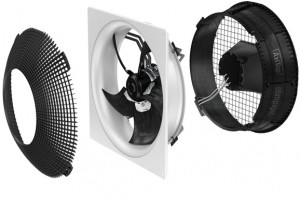
Figure 4: The diffuser reduces the noise generation in the medium-frequency range, and can be combined with the air inlet grille
Purchasers in the field of ventilation, refrigeration and air conditioning technology can take additional action regarding noise reduction: further optimisations can be achieved with the help of another passive component. If users take a fan and combine the air inlet grille described above with an “AxiTop” diffuser on the discharge side, this both increases energy efficiency and reduces noise emissions still further – above all in the medium-frequency range. This means that the FlowGrid reduces the deep-frequency range, while the AxiTop is responsible for a further reduction in the medium-frequency range. It is easy to grasp how this works: in fans with free outflow, the exit losses that result from the operating principle are frequently underestimated as an energy consumer. The diffuser can help minimise these losses. It operates rather like a reverse nozzle and significantly reduces the exit losses thanks to its pressure-increasing effect (figure 4). Efficiency is increased and the operating noise is simultaneously reduced.
Ideal operating conditions for fans
The acoustic improvement is primarily of interest when fans are in operation in environments where noise is a critical factor and the user additionally combines the diffuser with the air inlet grille (figure 5), for example when using a tested condenser. In this case, the outside air is drawn through a heat exchanger.The condenser is fitted with an axial fan that has a diameter of 800 mm and runs a diffuser fitted on the pressure side. The noise level can be reduced by an additional 3 dB(A) with the help of the air inlet grille.
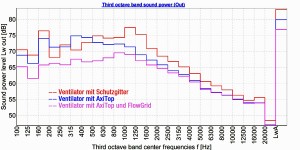
Figure 5: The combined use of the AxiTop and FlowGrid resulted in a 5.8 dB(A) reduction in noise emissions from the tested condenser, primarily in the low-frequency range
Thanks to the combined use of the AxiTop and FlowGrid, the noise level is reduced by 5.8 dB(A) and the tonal noise is reduced by 20 dB – any persons present will find this to be very pleasant. Like the air inlet grille, the diffuser is also made from light, resistant plastic and is easy to mount and retrofit. As it is only 250 mm high it is generally not necessary to change the design of the application, even for the purpose of retrofitting. Purchasers will soon be able to benefit from the advantages of noise reduction in the low-frequency range: FlowGrid models for size 500 and size 630 axial fans, which are the typical sizes for use in heat pumps, will be available in the first quarter of 2014. Versions for size 710 and size 800 centrifugal fans, as used in larger air conditioners, will also be entering series production soon; additional versions will follow. The AxiTop has already entered series production.
Using passive components – the diffuser and the air inlet grille – the Mulfingen specialists have once again succeeded in continuing the development of fan technology and setting new standards. The optimisation of inflow and outflow provides ideal operating conditions for fans, enabling energy-efficient operation that is as quiet as possible.
Hi
I need some details
Hi Mustafa,
Thanks for your comment, your request has been forwarded to our colleagues in Dubai, they will contact you.
Best regards, your mag-Team