The life span calculation generally applied to fans today is based on the assumption of statistical averages. For this, there are various calculation formulas and evaluation criteria for loads such as temperature, speed or dust and humidity. If operating conditions greatly deviate from the norm, this approach cannot provide any meaningful values for the actual service life of an individual on-site fan. In order to achieve a more reliable statement about the actual service life potential here as well, in addition to general laboratory findings, the actual on-site loads have to be measured during operation, added up and included in the calculation. A new diagnostic tool for fans collects the relevant data for this and calculates the individual remaining service life under the actual operating conditions. Thus operation and maintenance of difficult-to-reach fans are decisively improved and the reliability of the overall system increases.
Statistical statements are only as good as permitted by the assumed input data. Even the best calculation program is not able to provide any realistic statement about the service life of a product if the assumptions are incorrect. However, precisely with fans for exposed applications in a safety area or for systems that are difficult to access, such as cellular telephone stations on mountains, the most exact possible determination of (remaining) service life is important to the operators. Therefore it is ideal if the calculation includes the actual load of the individual fan where it is used. If this takes place right in the fan, and if the fan can issue an alarm signal when a configurable safety threshold is exceeded, that improves the reliability of the overall system. Therefore there is no need for any cost-intensive preventive replacements; that saves time, money and personnel.
Existing evaluation method
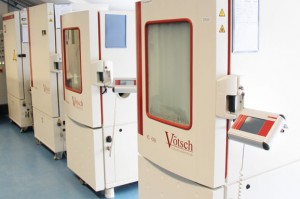
Figure 1: In the endurance test room – the data for the conventional life span calculation is acquired using the climate chamber.
Existing, conservative catalogue information regarding service life refers to an accepted, average operating point; for example, service life L10 of 70,000 hours at 40°C ambient temperature and 3,600 revolutions per minute. Therefore they are more of a standard value for the practical evaluation, since operating temperature and speed continuously change throughout the day and over the seasons, thereby affecting the service life. To this are added unforeseeable factors, such as dust or humidity, which are taken into account only in special cases in the laboratory. Usually, current evaluations of lifetime are based on laboratory testing with defined standard conditions for temperature and speed (Figure 1).
For theoretical considerations of statistics and testing, the average service life of the entire production is used. To achieve shorter testing periods, often the thermal load is also set unrealistically high in order to achieve faster ageing of the components. Changing operating conditions, which always occur in real-world applications, are not taken into consideration in this procedure. In order to make statistical statements concerning fans, it is enough to take into consideration the service life of the rotor bearing. Failures of the electronics or the motor winding are significantly smaller and can normally be neglected. On this basis, ebm-papst developed a diagnostic tool implemented in the fan that determines the individual service life of the fan while taking into consideration the respective ambient and operating conditions. This way the existing limitations of the operating statistics are completely redefined by exact fundamental data and the latest methods of calculation.
New approach
The new service life prediction takes into account the individual history of the fan in its respective operation and thus statements about an expected remaining service life can be made in individual cases using the application conditions. Changing temperatures (day/night cycles or seasonal fluctuations) are taken into account, as are the accepted dust pollution on-site and the actual speed. This data is used by the electronics integrated in the fan to calculate the service life (Figure 2). The new early failure detection is conceived particularly for users who can replace the fan only at high cost or at certain times (for example, remote measuring stations, radio buoys). With the new options, the replacement intervals can be planned in a timely manner or adapted to the individual requirements. Fans no longer have to be “preventively” replaced, which reduces investment and maintenance costs and increases operating reliability.
Real-world applications
Instead of operating on preset values, the new system uses data that is updated on an ongoing basis, such as operating speed, ambient temperature and downtimes. Basic data, such as the bearing design (ball or sleeve bearing), the type of bearing lubrication and the grease used, and other ambient conditions is preset. That way service life reserves can be used, since the current forecast always takes into account the overall history of the fan.
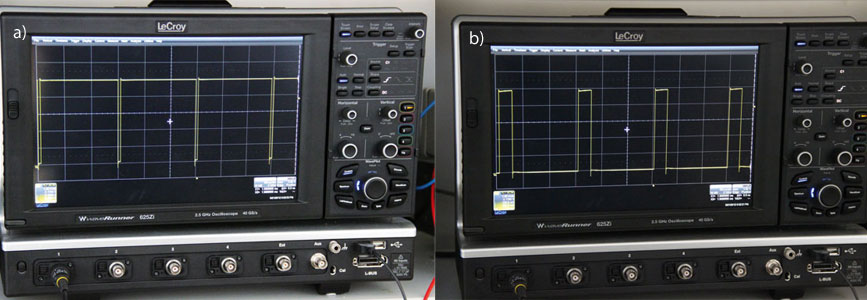
Figure 3a and 3b: The remaining service life can also be output digitally via a PWM signal a) high, b) low or as an analogue value via an additional RC element.
The diagnostics system is based on empirical correlations from real-world applications and decades of endurance tests under various conditions. Customer-specific output formats, such as L5 instead of L10, can be taken into account. The output can be wired out via either the alarm wire or an additional wire and can be called up digitally. The remaining service life can also be output as an analogue value via a PWM signal to an RC element. Thus the product can be used nearly up to the actual end of its life without losing reliability. That conserves resources, increases value creation and reduces costs of procuring replacements and maintenance costs (Figure 3a, b).
Service life or reliability
Service life and reliability are two terms that are often used and equally easy to mix up.
Service life, often abbreviated to L10, specifies a period in hours during which up to 10 percent of the devices will have failed. An L10 value of 100,000 hours means that 90 % of tested devices have reached this run-time.
In contrast, reliability is specified with the value Mean Time Between Failure (MTBF). Since fans normally cannot be repaired, a more apt designation would actually be MTTF (Mean Time To Failure). Despite this, MTBF has become the expression that is most commonly used. Statements regarding MTBF values only apply during the planned period of validity (e.g. usable service life). The failure rate can increase significantly after that due to signs of wear. A MTBF value of 1,000,000 h (more than 110 years) means that if 1,000 devices were running at the same time, one of them would fail every thousand hours, i.e. every 42 days (1,000 h * 1,000 = 1,000,000 h).
Leave a comment